It is no secret that manufacturers must focus on efficiency and productivity for success. The organization must provide the right information and tools at the right time to enable the workforce. With so many options available, separating the "must have" from the "nice to have" can be challenging.
LNS Research analyzed more than 900 responses received from industrial manufacturers to identify trends that significantly improve profitability. What stood out was that more than 70% of the most profitable manufacturers are either piloting or currently engaged in Future of Industrial Work (FOIW) initiatives. In addition, more than 80% of these industrial organizations have seen meaningful progress and delivered corporate value through these workforce initiatives.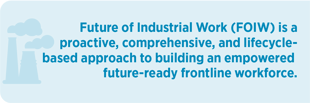
This blog will uncover how these manufacturers have significantly increased efficiency and productivity to improve profitability.
Profitable Companies See the Urgency of Change
Some manufacturing leaders believe that the frontline workforce labor challenges are abating and that natural market forces will drive us back to equilibrium. Over the last year, demand has decreased, and the workforce crisis hasn't been as drastic. The demand for goods will start to pick back up as interest rates begin to fall, and manufacturers will once again see a need to fill workforce voids.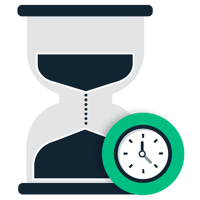
Unfortunately, less than 20% of Gen Z is interested in manufacturing. In addition, fewer than 30% of parents support a career choice in manufacturing. The pool of potential candidates continues to shrink, with only 38% of women pursuing STEM careers showing interest in manufacturing.
Our research shows investing in future-proofing operations during the downturn will strongly enable a company to outperform those who aren't. Manufacturers with significantly improved profitability are proven to drive urgency from the top, with workforce initiatives led from the executive level and considerably aligned to the business strategy. Those who are struggling either haven't formally defined responsibility, or it has fallen on the shoulders of the plant leader.
Building a Resilient and Adaptable Workforce is a Shared Effort
You might ask, if the plant leader shouldn't be responsible for workforce development, then who should be? Quite frankly, the manufacturers who are winning feel that it's everyone's responsibility. Over 40% have included workforce key performance indicators (KPIs) as a performance management success factor for every role considered.
The least profitable companies are most likely to include workforce KPIs when evaluating the performance of their executive leaders. In fact, only 6% of these respondents indicated that corporate roles have workforce KPIs as a success factor of performance management. This lack of focus on workforce development is poised to become a significant obstacle down the road, impacting productivity, innovation, and overall competitiveness in the industry.
Most companies will need to rethink the organizational makeup when defining the responsibilities for workforce initiatives. The most profitable companies have appointed the Heads of Human Resources (HR) and/or Learning and Development as those responsible for initiatives to improve employee productivity, engagement, retention, and development. We have already seen organizational changes and predict more manufacturers will create corporate workforce development roles such as a VP of Operations HR, a VP of Workforce Development, or even a VP of Employee Experience.
Accelerate Momentum by Aligning and Integrating Key Initiatives
FOIW initiatives are critical to build a future-proof workforce. Organizations should align workforce initiatives with other initiatives using the same approach as those companies that have significantly improved profitability with FOIW programs. Nearly 70% of companies with the most success have major and/or complete integration across four other programs.
Manufacturers should integrate workforce initiatives with existing EHS, Enterprise Risk Management, Unified Performance Excellence (UPX), and Autonomous Plant (Factory of the Future) Programs. These programs are most likely to have efforts directly targeting the workforce aligned with the organization's operational objectives to support the Chief Operations Officer. This may include implementing risk mitigation strategies and acting on workforce competency assessments to enhance operational performance and resilience.
Connected Frontline Workforce (CFW) applications play an essential role in improving a company's ability to attract, train, and retain talent. Stakeholders aren't just interested in creating a more sustainable workforce but one that is more diverse and inclusive for employees. Companies can be more effective by focusing on the total employee experience, strongly integrating initiatives across other programs, and leveraging the capabilities of CFW solutions to assess workforce engagement and culture.
Final Recommendations to Manufacturers
Manufacturing Leaders can no longer afford to focus solely on the success of back-office employees. Newer generations have already begun to join the workforce and these employees bring a whole different set of skills and motivators. Manufacturers should take the same steps as those companies who have significantly improved efficiency, productivity, profitability, and overall competitiveness:
Identify corporate-level responsibility for planning and defining workforce initiatives. Focus efforts on engaging and empowering employees across all facets of the workforce. Take a holistic approach that considers the contributions and needs of all employees, not just those in administrative positions. For many, this may include creating a new role to ensure success for the future of industrial work.
Implement robust training and knowledge management process capabilities. Leaders' knowledge management efforts are seeing significant improvements by implementing innovative, new training methods and practices to meet changing training preferences and increase employee competencies and skills. Align Workforce Learning and Development initiatives to business objectives and strongly integrate efforts with existing programs to avoid duplication of effort. Evaluating existing risk, safety, quality, and profitability factors can highlight the areas of opportunity to coordinate efforts.
Track employee engagement and effectiveness to prioritize actions. Define an operational architecture and data management practices that enable data to be collected and analyzed across the organization. Ensure that information from EHS, HR, IT, OT, UPX, and Quality systems allow newer technology to provide a whole new way to measure effectiveness and reassess the current way of working. Many manufacturers report that digital natives are finding innovative ways to do the work better using what's already in place.
Manufacturers must recognize that the need for change is urgent. An organization is only as good as the employees that work within it. Those who continue to rely on the ways of the past may find themselves forced to look for a future with another company. Learn more about how to empower and engage the frontline by following the LNS Research Future of Industrial Framework.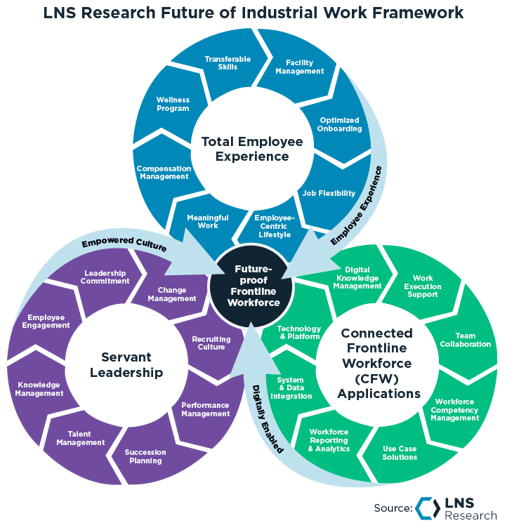
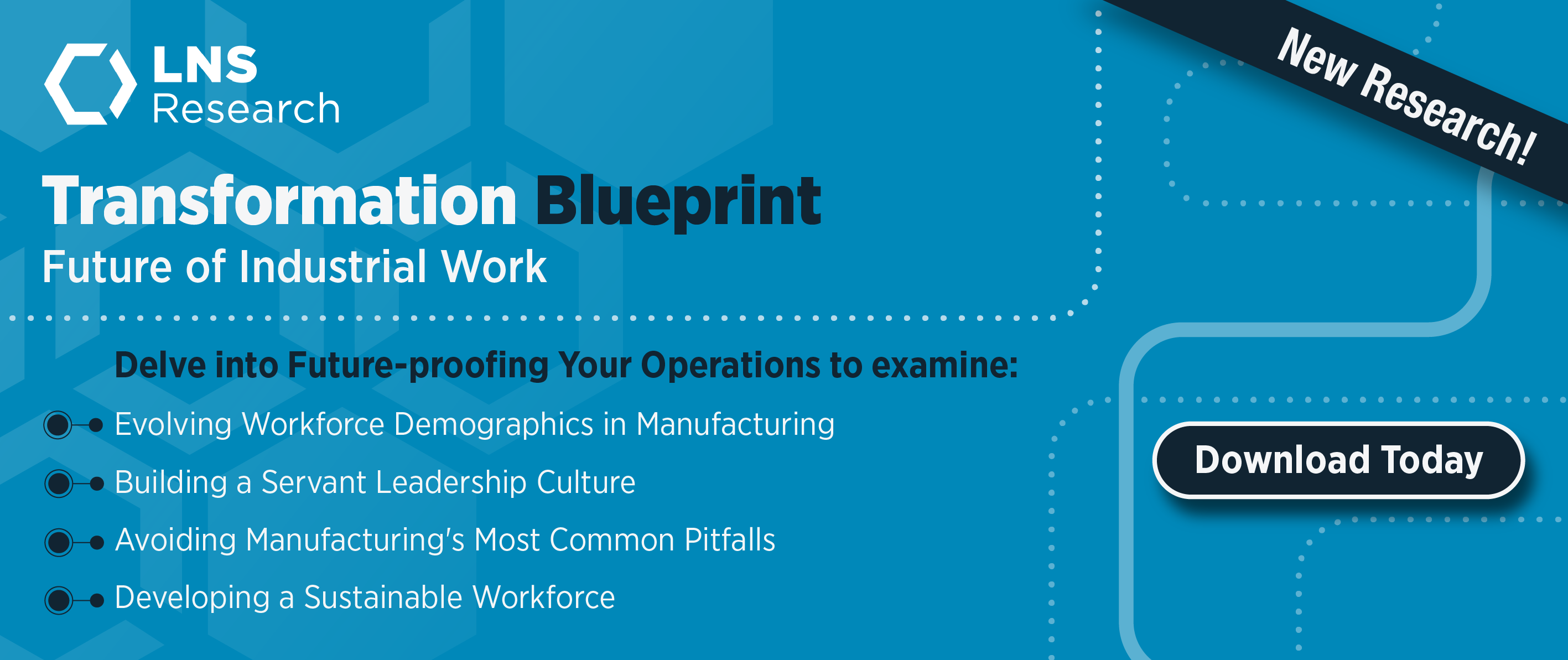