Safety culture has been a long-standing topic in environment, health, and safety (EHS) and operational risk management (ORM) for industrial organizations. It’s receiving more attention in recent years with increased recognition of the essential role of human capital management and organizational dynamics in running a successful business.
Click here to speak with Peter Bussey.
In my recent webcast, “Harness Organizational Culture for EHS and Operational Performance,” I suggested that it might be time to stop focusing on safety culture per se and start working on a culture of Operational Excellence instead to improve EHS and safety performance. Let’s dig deeper into this question, even if some might consider it to border on heresy.
Safety Culture: A Well-Established Concept
Use of the term safety culture goes back to the report on the Chernobyl nuclear accident published by the International Nuclear Safety Advisory Group (INSAG) in 1988. Its definition is, "That assembly of characteristics and attitudes in organizations and individuals which establishes that, as an overriding priority, nuclear plant safety issues receive the attention warranted by their significance.” A simple explanation that captures the spirit of the academic definition is “The way we do things around here.” That is, an organizational culture, whether safety-oriented or not, expresses itself by how decisions are made, and work is done day in and day out.
Since then an industry ecosystem has developed to help organizations assess and improve their safety cultures. There are many safety culture consultants and a large body of academic research on the topic. Numerous tools are available to assess safety culture, as are programs to improve it, and software to manage it. Many industrial organizations have invested significant amounts of internal and external resources, and in many cases attained good results. There are conferences focused solely on safety culture. There’s no question that safety culture is a valid topic and discipline, and that organizations have benefited by focusing on it.
Is Focusing on Safety Culture the Right Way to Improve Safety Performance?
LNS Research helps industrial organizations improve business and operational performance through an integrated Digital Transformation framework. The starting point is clarity on an organization’s strategic objectives based on its mission, vision, and values. Next comes realizing these objectives through Operational Excellence. We define Operational Excellence as aligning people, process, and technology capabilities to create a culture of continuous improvement to achieve strategic goals.
In our view, Operational Excellence success requires a cross-functional platform incorporating the domains of manufacturing, EHS, quality, asset, and energy management, among others. Only with such integration and collaboration can processes and performance be optimized, and an effective culture manifested. This approach is consistent with the long-held notion among EHS and safety professionals that one of the keys to success is business integration – embedding EHS and safety into the entire fabric of the organization from the boardroom to the plant floor.
If one accepts this view, it raises some questions. Why isolate safety culture from Operational Excellence culture? If safety and EHS management shouldn’t be run as departmental silos, then why should safety culture be managed separately? Wouldn’t it be more effective to position safety as being integral to Operational Excellence and work on it?
There’s No One-Size-Fits-All Approach to Safety Culture
Of course, there are no right or wrong answers to these questions. What’s right for one organization might be wrong for another. Many factors will influence the appropriate approach, including risk profile, current Operational Excellence and safety capability maturity, corporate values, and the state of existing organizational and safety cultures.
There is no one-size-fits-all approach to the role of culture in improving EHS and safety performance, and how to manage it. In high-risk industries such as oil & gas, mining, and chemicals, getting safety and ORM right tends to be mission critical to overall Operational Excellence. Such organizations often are at a relatively high level of EHS and safety capability maturity, with a high degree of business integration.
Take for example ExxonMobil. The company and its leadership recognize safety as a core value and the importance of an engrained safety culture. This culture is realized through execution of the Operational Integrity Management System (OMIS), an 11-element framework to manage safety and operational risk, notably with “management leadership and accountability” as the starting point. The integrated management systems drive continuous Operational Excellence improvement including safety performance.
On the other hand, an organization in a lower risk industry such as retail may not need something as heavy-duty as OMIS and might decide to start with a simple safety culture survey. Another organization may choose to use safety as the “tip of the spear” in an overall Operational Excellence initiative, like the approach that worked so well for Alcoa in the late 1980’s, led by CEO Paul O’Neil.
Taking Action
Regardless of risk profile, every organization should make the time and effort to assess current EHS and safety performance and capability maturity in the prevailing organizational culture. Based on that, determine the appropriate strategy for culture assessment and improvement. Whether the initiative is called safety culture, culture of Operational Excellence or something else doesn’t matter. Doing it does, so long as it doesn’t promote the perception of “safety” as a department, but rather as integral to the core business and its culture.
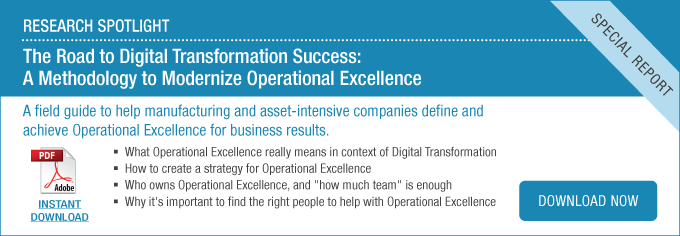