Manufacturing Operations Management (MOM or MES) systems have been commonly implemented in batch and discrete manufacturing plants for many years (Early MES was implemented in the 1980s). The benefits to automation, control, and business are well understood but the number of manufacturers implementing MOM has remained constant in our surveys over the last years at around 20% of factories. There is a multitude of reasons, often focused on the gap between expectations and reality; for example a company might implement one factory and then judge the cost and time of rolling out 20 more completely prohibitive. We have consistently been promised more for less and yet we are still being led down the same path. Things are changing; in this blog we will look at some of the trends that are going to help manufacturers overcome these challenges in the coming year or two.
Seventh Life of MOM - Refined
Almost four years ago, I wrote about the seven lives of MOM, a vision into the future of MOM architecture and how it would be deployed. The 7th life was defined as “No MOM” where the functionality previously implemented in MOM systems would be distributed as apps across an Industrial IOT (IIoT) platform. This still seems like a good idea to most and the reality is getting closer.
LNS’ research on Industrial Transformation (IX) platforms demonstrates that the operational, and in particular data, architecture required to support IX will include everything needed for MOM.
Now, all we need is functionality via apps. The good news is that many IX platforms support sophisticated analytics apps, the low hanging fruit of IX, and operational apps are becoming available on some IX platforms. We believe that 2021 will see a step change where third party app developers will deliver apps on the major IX platforms. Many IX platforms claim to be open and this will be a test of that claim. With the advent of low code/no code development suites, the possibility to build a flexible set of MOM functions held together through low code apps will change the way we develop MOM.
Digital Lean
Lean manufacturing has been around considerably longer than MOM and is central to many manufacturers’ continuous improvement programs. Traditional Lean focuses on manual recording of events and on the shop floor interaction. With IX platforms all of the data required for Lean processes can be made available across the enterprise. It is not just a matter of making lean processes digital; the advantages that digital offers can change the way you implement specific lean processes. Let’s take the Gemba walk as an example.
Traditional Gemba walk involves setting out to the shop floor so managers and leaders can have open and respectful ad hoc meetings to address problems at “the actual place” (Gemba in Japanese). Many people who are trying to introduce digital to Lean will make digitized reporting on handheld devices so they can learn and get feedback from the shop
floor without actually going there. This type of solution will not aid the conversion of traditional Lean practitioners. Rather, we should consider the essence of Gemba and use digital technology to improve it; when a leader goes on a walk, he/she is fully prepared with his digitized information (otherwise known as his/her tablet) to focus on the known issues, to record decisions and to set up follow up actions for improvement and feedback on the next Gemba walk. It is easy to demonstrate that the new Gemba walk (walk included), is a better process than the old one and that we can use the new tools to improve the Gemba process itself.
Cobots in the Time of COVID-19
The COVID-19 pandemic has changed the way we live and work. Social distancing is an effective way of reducing the spread of the virus but does not make manufacturing any easier. Many production facilities have high concentrations of people for complex tasks and are having to reduce flow (and perhaps overall takt time) to meet the worker separation required by COVID-19.
Collaborative robots offer the possibility to work alongside humans without guards in place so they can interact closely. However, getting everything to work well and deliver the productivity required is far from trivial. For each cobot installation, everything including heads and tools attached have to be considered when defining “safe.” It is the whole installation, including humans, that has to be made safe. Many cobots have advanced configuration facilities that allow configuration by teaching and manipulation, and this can help to assure that all movements are safe.
The spread of such a devastating virus will help the cobot industry to expand their footprint, not just for worker distancing but across many processes where they can improve productivity and make the work environment safer and more pleasant.
Additive Manufacturing
Our final trend to look out for in the Factory of 2021 and the future is 3D printing, or additive manufacturing. We continue to see big investments in the technologies, especially in materials and speed of printing. However, real break-out in the industry is still in areas such as mass customization and personalization of consumer wearables and components. Many opportunities are in complex discrete manufacturing where volumes are low and part integrity is high. Many of these opportunities are in the aerospace industry that is not likely to see large new investments in 2021. However, we will be following the industry with interest – possibilities are endless and 2021 might just be the year for additive.
There is no question that 2021 will be a stand out year for manufacturers. Recovery from Covid and the rapid advance of industrial transformation (IX) with its advanced data architectures will enable the changes needed to encourage these trends. All manufacturers should be considering them and, most of all, they should become champions of IX.
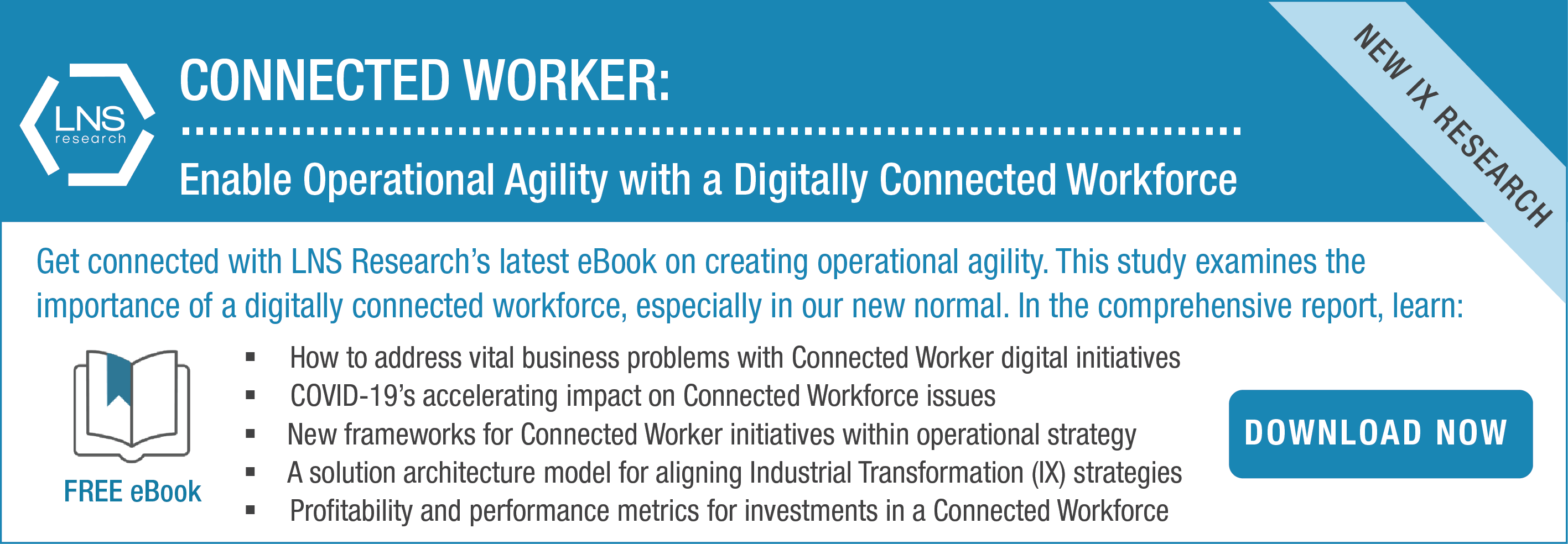