NPI Essential for Business Results, Yet Generally Ineffective
New product introduction (NPI) is a linchpin process in most corporations and industries. NPI is key to competitiveness, revenue growth, and customer retention. Given the importance of NPI to overall corporate success, it’s no surprise that manufacturers devote considerable cost and effort to it. According to our most recent data, the median manufacturer involves 25% of personnel in NPI and has a new product cycle that lasts 24 months on average. Despite the substantial investment, NPI often fails to deliver expected outcomes. Forty-four percent of NPIs fail to meet all or even most success criteria.
Unsurprisingly, there’s a long list of challenges around NPI. What is surprising is that 14 out of 19 NPI challenges are core process deficiencies ― deficiencies within every company’s power to change.
The question becomes: why would any company allow these process challenges to persist? Our research data along with anecdotal evidence reveal four paramount issues.
ISSUE #1 | NPI is about process, and that’s not exciting or sexy. Most companies would rather invest in new technologies, create and fill new roles (think chief digital officer as an example), or contemplate new business models instead of document, institutionalize, and continually improve processes. (Remember how long it took the market to widely adopt Lean, even after its impact was documented.)
ISSUE #2 | NPI is (or must be) a cross-departmental and enterprise-wide effort, yet deployed applications are (almost always) siloed by department. Corporations have historically invested in only one facet ― yes, an important one ― of NPI: product development/engineering/R&D. That investment is generally necessary but insufficient. Having a great a product design discipline does not automatically introduce the collaboration required with the manufacturing, quality, and supply chain organizations. Compounding the disconnects, manufacturers seldom integrate suppliers procedurally into the process.
ISSUE #3 | Technology solutions exist in silos ― they have been built for and bought by individual departments. Finance buys financial applications and enterprise resource planning (ERP). Engineering buys computer-aided design (CAD), modeling, simulation, and product lifecycle management (PLM) systems. Manufacturing buys MES/MOM, distributed control systems, automation, and asset performance management applications. Quality buys corrective action/preventive action (CAPA), compliance, and traceability apps. No one should be surprised by this: nearly every company divvies up the capital budget by department and tech companies follow capital budgets. Ultimately, collaborative processes across functions are seldom automated.
ISSUE #4 | Quality handicapped by lack of clout. This is the one group with the most holistic view across the NPI process, yet these people don’t have sufficient influence within the industrial enterprise. Quality ― if it’s doing its job fully ― looks at issues across design, manufacturing, supply chain, and all the way out to consumer acceptance and feedback. Meanwhile, seldom does it have a leadership role in the corporation.
Improving NPI: The Way Forward
Fortunately, recent research reveals the way to break this dysfunctional cycle. LNS Research discovered what it takes by studying Industrial Transformation programs generally, and Quality 4.0 initiatives specifically. The evidence shows that IX is paying off, and Quality 4.0 initiatives are driving improvements in quality, manufacturing, and NPI metrics.
When we examine NPI metrics specifically, we find that supplier quality management (SQM) is critical to improving this vital function in most industries. As we drill into how companies deploy supply chain quality and collaboration technology, we find that:
- Companies that automate SQM report 10-point better NPI scores (to achieve time, volume, and quality goals) and 14% more of their NPI launches meet all success criteria.
- Companies improve NPI by an average of 33% with each of six Quality 4.0 connected supplier use cases. Evidence of meaningful improvement is independent of a company’s starting quality maturity (e.g., companies of all maturity levels improve).
- Leaders in the deployment of Quality 4.0 connected supplier use cases have 22% better NPI scores than average manufacturers.
- Improvements in NPI correlate closely with improvements in quality and manufacturing. Leaders in NPI are also 21% better in quality metrics and 4.7% better in manufacturing metrics.
Impact of SQM Pervasive Throughout the Enterprise
Interestingly, we find that a specific focus on supplier quality can be a Rosetta Stone to improve performance across the organization. Let’s examine the impact of SQM on just a couple of the issues mentioned previously.
SQM Impact #1: Process Challenges
We can all agree that NPI processes usually span the enterprise (e.g., many or most departments) and multiple organizations beyond the company. However, most industrial companies lack even fundamental NPI process practices, resulting in poor repeatability and monitoring. Only 29% of companies have standardized/harmonized the NPI process across the corporation. Overall, 18% of companies report having robust, standardized processes for supplier quality management.
Institutionalizing NPI processes across the enterprise and the supply chain has a marked improvement on NPI. Cost of poor quality, for example, goes down by 16% among companies that formally adopt more than one of these supplier practices. As a result, the manufacturer can support more new product launches while still increasing the percentage of NPI’s that are successful (by as much as 62%).
Automating NPI practices provides additional improvement. We consistently and repeatedly find that companies that automate supplier quality processes achieve higher business performance. When we examine four types of collaborative quality processes (change management, risk management, supplier quality management, and statistical process control), we see positive and escalating results in key metrics. These numbers show that automating supplier quality processes is one key way to become best-in-class in NPI.
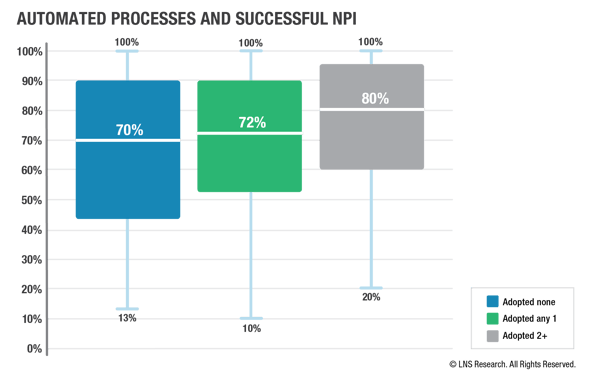
SQM Impact #2: Department, Enterprise, and Tech Silos
Yes, focusing on supply chain quality management practices has direct positive impact as illustrated above, and helps build cross-functional and enterprise-wide discipline. More than that however, it breaks down the barriers caused by silos. There is real and tremendous business value in institutionalizing and automating NPI and supplier quality practices. The “spillover” effect is equally real: when an organization focuses on these processes, it can reveal the value and capabilities needed to succeed in collaborative processes more generally.
While the engineering/R&D/design function is highly automated with a plethora of CAD, PLM, and simulation tools, the cross-functional work of NPI is often largely not automated. Enterprise quality management systems, supply chain management, and business process management tools are not widely deployed across industrial organizations in support of the NPI function. Still, the value is strong, especially to address the collaborative requirements between design and the rest of the organization engaged in NPI activities.
Therefore, investing in EQMS and supply chain quality can be a critical mechanism to reduce the technical barriers to overall collaboration in NPI.
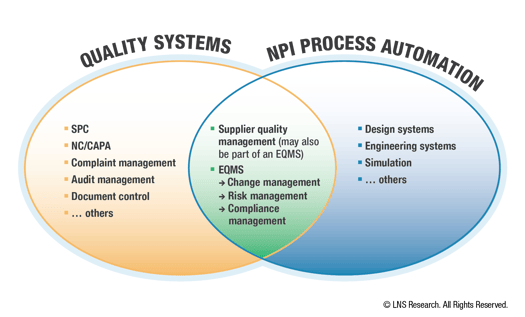
SQM Impact #3: Elevate the Role of Quality, From Department to Leader
A focus on NPI generally and supplier quality specifically triggers a powerful change in the role of quality in the enterprise. The most fundamental transition is the shift from quality as a standalone process executed by a low-profile department to become a core part of the corporation’s fabric. Many companies view quality as a necessary evil and/or an insurance program. Now however, quality has the opportunity to engage more directly in the business. Quality leaders drive business results by reducing costs and improving quality and the customer experience. In turn, quality earns a higher status within the organization.
Quality Leader: Get in the Driver’s Seat
Can a company achieve NPI results without the help of the quality leader? Of course, it can. However, the quality organization has unique skills critical for NPI success, specifically around formalizing and institutionalizing processes. Therefore, quality teams must take an active leadership role in NPI, SQM, and Quality 4.0. Quality applications like EQMS and/or SQM are essential to automate the collaborative portion of NPI.
Quality leaders certainly find the research compelling: IX and Quality 4.0 early adopters achieved dramatic results for their efforts. They improved product quality, are meeting customer needs better, and have improved business performance. Those on the forefront created competitive advantage by aggressively pursuing transformation and digitalization. The bottom line: companies should take IX steps now or risk losing ground to competitors.
If your company wants to accelerate and improve NPI, supplier quality and connected supplier use cases can be the best place to start. Efforts to improve NPI, particularly supplier quality management, have significant benefits in NPI but also in quality and manufacturing. Further, SQM helps build a culture of quality and collaboration, which is critical to continuously improving NPI, quality, and manufacturing performance.