Industrial Transformation (IX) is the proactive and coordinated approach to leveraging digital technologies to create step-change improvement in industrial operations. Industrial Transformation has become a genuine phenomenon across industrial operations. Over two-thirds of companies surveyed have implemented, are currently implementing, or plan to implement an Industrial Transformation (IX) program. The worldwide COVID pandemic is not slowing IX down, with 78% of companies maintaining or accelerating their programs in the face of the economic turmoil created by the pandemic. IX Leaders are three times more likely to be increasing their IX budget in the face of the pandemic.
We define the top 20% of those companies executing transformation as IX Leaders. Early IX adopters realized significant Return on Investments (ROI) from their IX Program. As detailed in a recent LNS Research eBook entitled, Maximizing Payback with Best Practices from Next-Gen Leaders, IX is delivering for manufacturers. ROI is being realized widely across IX Leaders. In fact, 80+% of IX Leaders were able to reduce COGS, and/or improve operating margins, and/or grow revenues by at least 3% as a result of their IX program.
%20Leaders%2c%20Benefits%20from%20IX%20Program.png?width=820&height=199&name=Industrial%20Transformation%20(IX)%20Leaders%2c%20Benefits%20from%20IX%20Program.png)
If you are a regular reader of our blog, you know LNS Research has been studying IX for years. Our most recent research, a global survey conducted in the winter of 2021, illuminates the five stages of IX. The chart below highlights those stages. Our findings indicate that IX Leaders are in the Scale or Embed stages of IX. As such, we've recently released a research spotlight entitled Industrial Transformation Readiness: "Getting Real” covering the latest findings. Let’s look at each stage of IX and the core goals and methodologies.
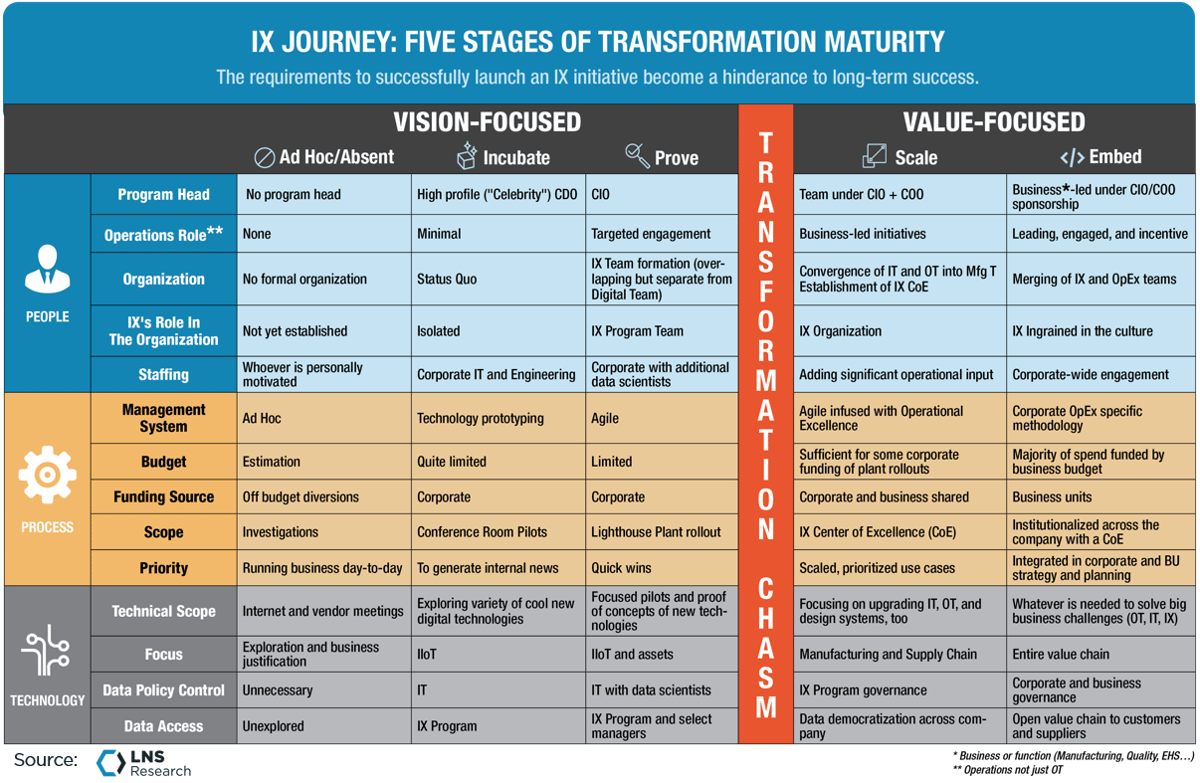
Ad Hoc/Absent
Everyone must start somewhere. The beginning stage is all about getting to a decision and a commitment. The executive leadership of the company must decide IF they want to seek out step-change improvements in operations. Getting to that decision usually involves a lot of discussions, evaluation of competitors, technology sampling, financial modeling, and updates to corporate strategy. Two core deliverables come out of this stage:
-
-
-
A commitment by executives to the success of Transformation (the value of that commitment is critical), typically realized in
-
The formation of an IX program with goals, metrics, budget, resources, and marching orders.
Interestingly LNS Research has found that this stage is foundational to the success of IX even if it has not started yet. We have repeatedly found that “real” executive commitment is fundamental to success and that many companies start programs – for whatever reason without a “real” commitment by executives. This leads to stagnation and often outright failure.
Incubate
Virtually every industrial enterprise that is initiating transformation is doing so by forming an Industrial Transformation program (IX program). LNS Research has found that the industrials are organizing their efforts in three to five-year programs with 12 different initiatives on average. There is no effective alternative than to kick off a special program initially. Resources need to be marshaled, specialized resources recruited/developed, and strategies created and adopted. A program team is the easiest and most effective way to get going.
The fundamental goals of the program at this nascent stage are two-fold. The first is to generate internal news communicating to the company that something important has been kicked off. Many industrial enterprises have initiated the program with an external hire, often from a technology company. The appointment of a high-profile executive from a technology company, a “Celebrity CDO”, signals to the organization that something different is happening here, that the company is committed, and that going digital is vital to the corporation’s long-term success. Second, virtually every manufacturer focuses this initial stage on testing technology. Conference room demonstrations and/or pilots abound as the small initial team seeks to learn and leverage technologies.
Prove
Quickly, IX Programs need to progress from PowerPoints, and a communications focus to actual implementation success (even if small). Therefore, IX Programs look for quick wins. At LNS Research, we are regularly asked about which use cases are the “low-hanging fruit” and offer the “best bang for the buck” (we have published the definitive answer to this question previously.) These quick-win solutions are generally deployed at the most technically advanced “lighthouse” plants because of their willingness and capability to deploy advanced digital technologies. Focusing on these easy opportunities and low-hanging fruit kickstarts the program and builds value.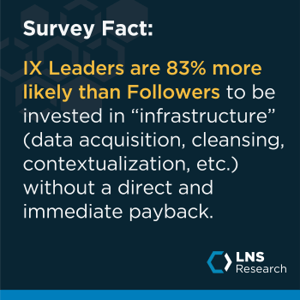
The team is growing at this stage usually with an emphasis on IT professionals, particularly data scientists and sometimes data engineers.
Scale
This is the first stage where industrial organizations are “getting real” about their transformation. Deep and wide engagement with operations personnel becomes central to the program. A focus on the tough stuff - key “infrastructure” work associated with the transformation that has neither quick returns nor direct payoff – begins in earnest. IX Leaders are 83% more likely than Followers to be invested in “infrastructure" (data acquisition, cleansing, contextualization, etc.) without a direct and immediate payback. The program goes beyond a focus on digital technologies to pursue upgrading/rearchitecting OT, IT, and design systems.
The organizational implications of transformation become paramount. Programs look beyond OT and IT technical convergence to organizational convergence. How to structure the role of Continuous Improvement (Lean, WCM, Six Sigma, etc.) teams in IX becomes a focus. The program team reorients its strategy away from focusing on “lighthouse” plants to focus on the development of an IX Center of Excellence (CoE).
Embed
This final phase rejects the program structure overall. Instead, the company seeks to work transformation into its standard operating procedures and across the company. Companies at this stage stop talking about the IX “journey” and focus on building the IX culture.
Introducing the Transformation Chasm
Our chart highlighting each stage of IX has a bright bar down the middle. And the stage after that bar is labeled "Scale". The bar and naming are very deliberate on our part. The bar represents the Transformation Chasm. The team staffing, processes, strategies, and methodologies that are needed to get an IX Program going become a burden to long-term success. Manufacturers cannot just refine the structure of the IX Program as it matures and delivers early results. Manufacturers must rearchitect their teams, processes, strategies, and methodologies. The gap between what is required to initiate a program and what is required to sustain and scale transformation – the bright bar – is the Transformation Chasm. To achieve the type of business benefit delivered by early IX Leaders, companies must forsake much that has worked for them in the early stages to cross the Transformation Chasm in mid-flight.
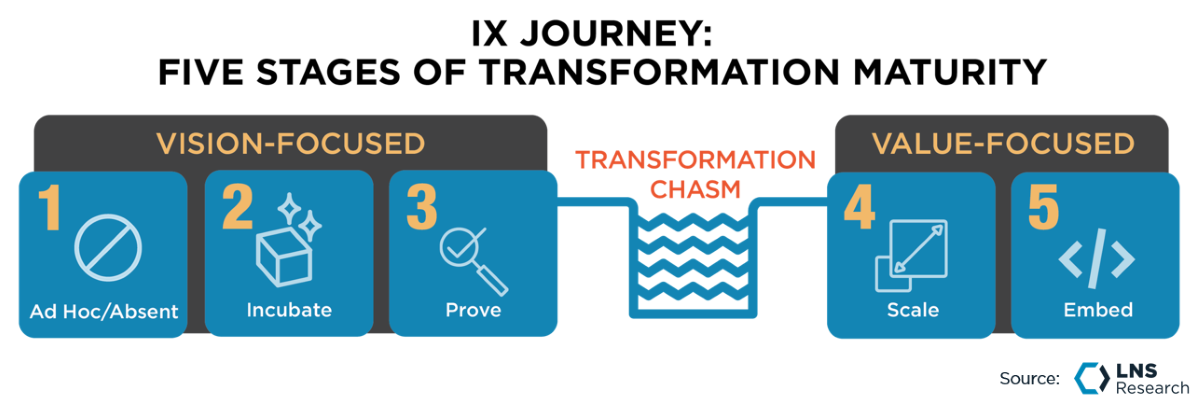
Chasm Purgatory Not Pilot Purgatory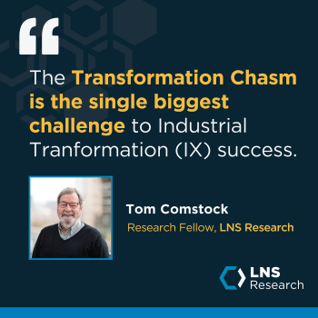
In a recent blog post, we note that “Pilot Purgatory” is fake news. Instead of the failure to roll out and scale technology being the key issue in IX today, LNS Research believes the Transformation Chasm is the single biggest challenge to IX's success. IX programs are churning, and many are failing to deliver the level of business benefit being realized by IX Leaders. But, the failure is not pilot purgatory. The failure to move out of the pilot stage is, in fact, a subset of the bigger challenge that companies must realign their programs – in mid-flight – to progress into the more mature and more impactful stages of Transformation. It is not a coincidence that we named the stages after the Chasm as “Value-Focused”. The money in IX – the positive impact on the financial performance of the company in the form of increased revenues, lower Cost of Goods Sold, and increased operating margins – is realized primarily in the last two stages of Transformation. And we know most manufacturers are not that mature or worse, have created IX programs that are oriented towards building vision but not real success.
Implications for Manufacturers
Recognizing the different priorities, goals, and strategies at each stage of transformation allows industrials to plan and execute their IX strategy more effectively. Further, by knowing where you are heading and the pitfalls in front of you – including the Transformation Chasm – manufacturers can align their program to the best practices evidenced by IX Leaders. For a detailed look at how IX Leaders are distancing themselves from IX Followers, check out our eBook on the state of IX Readiness. To understand the challenges of the Transformation Chasm and the roadmap for crossing it, dig into our Research Spotlight detailing the Transformation Chasm. The two sets of research lay out the best practices for IX and provide a primer to IX success. And, as always, stay tuned to LNS Research for the latest in Industrial Transformation.
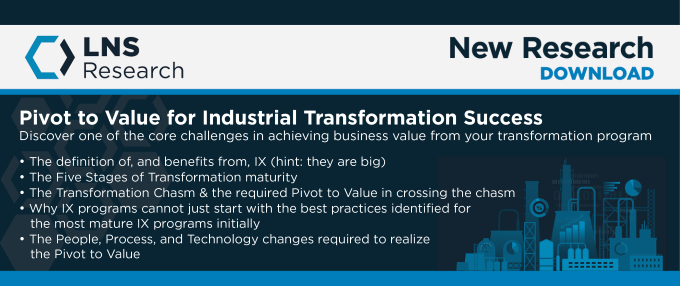
All entries in this Industrial Transformation blog represent the opinions of the authors based on their industry experience and their view of the information collected using the methods described in our Research Integrity. All product and company names are trademarks™ or registered® trademarks of their respective holders. Use of them does not imply any affiliation with or endorsement by them.