LNS’ Industrial Transformation Framework, has at its center, the Operational Architecture (OA) process where organizations align people, process, and technology at the convergence of IT and Operational Technology (OT). Ideally, OA efforts occur after a company defines its strategy and determines how technology should drive Industrial transformation.
In practice, however, LNS finds most companies back into an OA effort when building a business case for a transformation project. As companies try to define the scope of their manufacturing execution system (MES), enterprise quality management software (EQMS), asset performance management (APM), environment, health and safety (EHS) or other projects they realize the intersection of all the other areas of Operational Excellence with their chosen endeavor are becoming quite messy and complex. It is then when organizations realize that in today’s digital environment no system stands alone; they need to figure out exactly how all the technology will work together instead of creating silos, which will fight each other in delivering transformative value to the enterprise. The question then emerges, at what point does an initiative force the need to pursue an Operational Architecture effort?
>Click here to speak with Dan Miklovic.
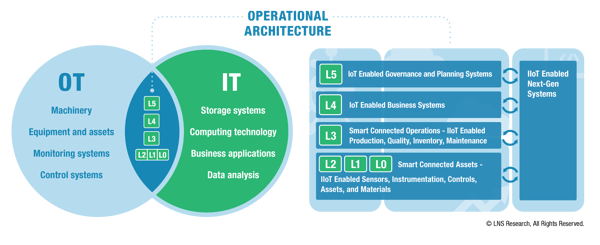
Digital Transformation becomes Industrial Transformation when companies recognize the real power of digital technology - break down organizational silos to let businesses operate holistically. When you optimize across the entire system instead of just each silo optimizing around its objectives, the ability to drive maximum financial performance becomes much more likely.
Operational Architecture Objectives
The first step in making a change, however, is recognizing that change is necessary. Not every OT project that an organization undertakes is likely to trigger the recognition that an OA exercise is needed. In some cases, the projects are so narrow in scope, they will have minimal impact on the other elements of the organization, and rightfully so. In other cases, there is the assumption that the scope will have minimal impact, but the reality is it will have a far more significant effect than assumed. Finally, there are the projects the organization recognizes as having a broad impact, but the assumption is that everyone understands that impact and is fully bought into the plan.
This leads to the $64,000 question: How do you pick the right initiative to drive an OA effort? It’s important to understand that the OA exercise has three primary objectives:
Later it becomes a matter of evaluating the initiative, be it MES, APM or even something as far-reaching as to assess the impact of an alternative process control approach such as OPA, and determine if the initiative will:
- Interface with plant floor devices, control systems or other OT and IT solutions like ERP, HR or SCM.
- Have multiple users in operations and specialized functions like quality, maintenance or EHS, and will be used by management to make operating decisions.
- Displace old systems with Industrial Internet of Things (IIoT)-enabled technology that can drive Big Data opportunities.
- Require new procurement models and likely introduce vendors into the ecosystem that is entirely different than in the past.
- Be mission critical to achieve production targets or to meet risk management objectives.
If your initiative requires any of these conditions met, and there is no ongoing OA effort or a team dedicated to managing the IT/OT intersection, then this is probably the right time to step back and institute an OA effort.
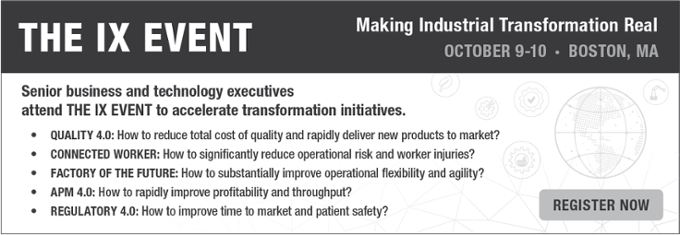