In this post, part 1 of 3, we will give an overview of the OEE Formula. In future posts we will go through an example of the formula, discuss how to use it for improved decision making, and examine what the OEE Software vendor landscape looks like today.
Defining the OEE Formula
OEE stands for Overall Equipment Effectiveness and is an important metric for many companies initiatives in Operational Excellence. There are many different definitions of OEE but it is largely understood to be a composite metric based on three different areas of a particular assets' performance. These three areas are: Availability, Efficiency, and Quality. This gives us the following OEE Formula:
OEE = Availability x Efficiency x Quality
The differences between OEE formulas come between how each of these 3 terms are measured, so it is important to be precise in this regard. At a high level it is helpful to think and talk about OEE in the following way:
- First, OEE measures how often an asset is available when it should be producing product for a customer
- Second, when an asset is producing product for a customer, OEE measures how close the asset is producing to it's theoretical maximum.
- Third, for those products that are produced, OEE measures the percentage of products that are produced within quality specifications.
Now let's see what that looks like for each term at a more detailed level.
Availability
Of all three terms, Availability has perhaps the most discrepancy between companies. Many companies advocate for Availability to be based on a 24*7 schedule. There are benefits to this approach and drawbacks. One of the main benefits is that it doesn't allow for variability or manipulation at the plant level, every asset is measured against the same standard. The draw back comes when one considers the implications this has on the supply chain. If there is no customer order and a company tries to maximize OEE this requires the company to produce product when there is no demand. Not necessarily an optimal use of the assets.
For this reason, LNS advocates measuring Availability only when a customer order is present (or a safety stock level needs fulfilling in a make to stock environment). When a plant is at capacity, this definition gives the exact same scenario as 24*7. When there is slack in demand, this definition does not penalize the plant.
Availability = Asset Uptime / Asset Scheduled Production Time
Efficiency
Efficiency can again create some discrepancies between companies. The main issue with Efficiency is if a company should use the theoretical maximum performance of an asset or the MRP specified attainment of an asset. Based on past experiences, there are again benefits and drawbacks to each approach. Using MRP attainment numbers can help keep production schedules in line with supply chain planner expectations. Unfortunately, it also allows for manipulation and differences at the plant level.
LNS Research believes the better approach is to use a theoretical maximum based on engineering or OEM estimations, which eliminates differences between plants. However, it should be noted that this approach can create inventory flow issues for companies that do a lot of MRP manipulation at the plant level. In the long run, consistency and OEE improvements will also improve supply chain planning performance but short-term growing pains can be expected along the way as local manipulations are slowly eliminated. Taking a theoretical maximum approach to Efficiency gives us the following formula:
Efficiency = Total amount of product produced / (Time asset was available * Theoretical maximum production rate of asset)
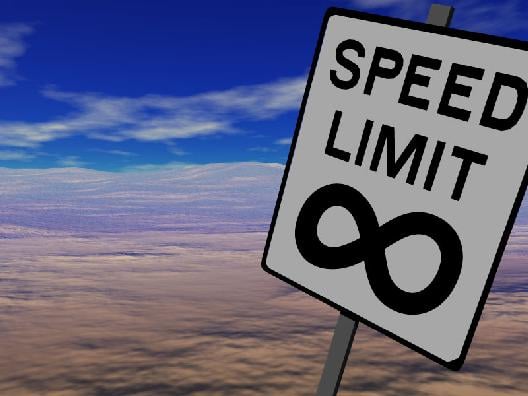
Quality
The final piece of the OEE puzzle is Quality. Usually quality is pretty cut and dry, a product hits a specification or doesn't. However, experience shows there is still some room for confusion. One of the major differences in how companies measure Quality is if they use Overall Yield or First Pass Yield. Basically, the different approaches account for rework in different ways. Based on our experience, when Overall Yield is used it often hides a lot of sins at the local level. For this reason, we advocate for using First Pass Yield not Overall Yield, giving us the following definition:
Quality = Total products achieving quality specifications first time / Total products produced
Closing Thoughts on the OEE Formula
The reasons given above for developing the OEE Formula in the way we have are indicative of our overall view on how OEE should be used and what OEE represents. Overall equipment effectiveness should be a standardized tool that doesn't allow for individual plants or decision makers to hide sins. Instead, OEE should maximize performance through highlighting areas of focus for continuous improvement efforts. However, this goal has to be tempered by the need to ensure maximizing OEE is in alignment with overall supply chain performance.
Hopefully this version of the OEE Formula will help companies start to measure overall equipment effectiveness in a more standardized way. Based on prior experience, companies using different OEE Formulas can have widely different OEE scores even though actual performance maybe very similar. It would not be unusual for a World Class plant to have a 60% OEE or 90% OEE depending on which versions of the OEE formula is used.
If you would like to read more on the topic of quality management, please click the button below to become a part of our community and gain access to our Quality Management Systems Research Library.