Asset Performance Management (APM), like so many other evolving enterprise applications is beginning to move to the cloud. The advanced analytics and the big data aspects of asset reliability are well-suited to amalgamation in the cloud. The level of confidence in a prediction is often dependent on the quantity of the data used to make the prediction.
Using the data from three lathes in your plant to predict reliability is possible but using the data from thousands of lathes in operation around the world adds a whole other layer of confidence in the prediction. This is the reason so many manufacturing equipment OEMs are beginning to offer reliability services as part of their product offering.
Also joining the fray are the traditional providers of reliability and Condition-Based Maintenance (CBM) software that have realized by aggregating data from all their clients, they too can improve the quality of their analytics.
As the Internet of Things (IoT) continues to proliferate, ever-increasing amounts of data will be available. And with the seemingly unlimited computational capacity available in the cloud, the growth of APM analytics in the cloud is a foregone conclusion. This leads to both new business opportunities and challenges, and in this post we’ll inspect both sides.
IoT and the Cloud Open Up New APM-Based Business Opportunities
Adding extra value to the products being sold is not a new concept. Manufacturers have continually added features and functionality to their products to create product differentiation as well as higher cost models with improved profit margins.
As noted above, one of the value-added services OEMs are beginning to offer is PdM-oriented analytics. As the designers and builders of manufacturing equipment, the OEMs generally are in the best position to use performance data from a machine to predict that machine’s reliability. With downtime having significant impact on profitability, particularly in organizations practicing lean methodology, improving machinery reliability can add significant value.
Another aspect of this is that with the increasingly rich data driving improved predictability of reliability, the opportunity to offer new services emerges. Some Fortune 100 suppliers like GE, Caterpillar, and John Deere have been offering capacity such as pounds of thrust (from GE’s jet engine group), tons of earth moved (Cat) or acres of ground plowed (Deere) for some time now. The risk for smaller manufacturers has been in pricing such an offering consistent with the risks involved. Larger manufacturers typically have had better data and could mitigate risks and price accordingly, so did the early entrants into offering services that were based on the function of the capital product that had been sold in the past instead of actually selling the product.
But with the IoT and cloud-based predictive analytics, even small OEMs can reduce their risks and price their services competitively. In addition, with the rich information they can get from the sensors on their equipment they can provide specialized services with highly skilled technicians far more economically than the end-user of their products likely could. This creates a scenario where the actual ownership of the asset may be retained by the OEM. In such a case, the OEM probably owns the asset performance data unless contractually specified otherwise.
When the OEM Provides the Knowledge Who Owns the Data?
The issue of ownership gets more complicated when the end-user owns the asset but sends the data off into the cloud to be aggregated with data from other manufacturers using similar equipment in order to get better predictions of reliability. In these situations things get a little muddier.
Since the data is aggregated it clearly does not all belong to only one of the sources. As long as the data is purely machine performance-centric it seems obvious that both parties have an interest and maybe shared ownership. But, when the data is production-centric, which may be necessary to perform the proper analytics, it becomes more complex.
As a manufacturer, the feeds and speeds of my manufacturing operation may well be highly proprietary and actually the driver behind my competitive advantage. Most manufacturers would certainly take exception to their information belonging to anyone but themselves, especially if they also own the production assets. Where they are just buying the capacity from the OEM, it becomes a bit more fuzzy.
As with many technological advancements, privacy and data ownership issues may well be more complicated to manage than the technology itself. As individuals we have typically given up a fair amount of privacy by using social media like Facebook and LinkedIn. However, in the business world there still remains a tendency to be more conservative when it comes to data ownership.
As manufacturers start moving data to the cloud for analytics, particularly as that volume of data grows through the use of the IoT, they need to carefully consider the data ownership issues. APM has proven to be the most mentioned verifiable value proposition of the IoT and will likely be one of the most active functional areas where the IoT is deployed so expect the ownership of data issue to come to head over APM early in the game.
Don’t take it for granted that if you own the asset you own the data. And, if you are buying capacity instead of the actual asset, make sure you have taken appropriate steps to protect your production data even if the asset performance data belongs to the OEM.
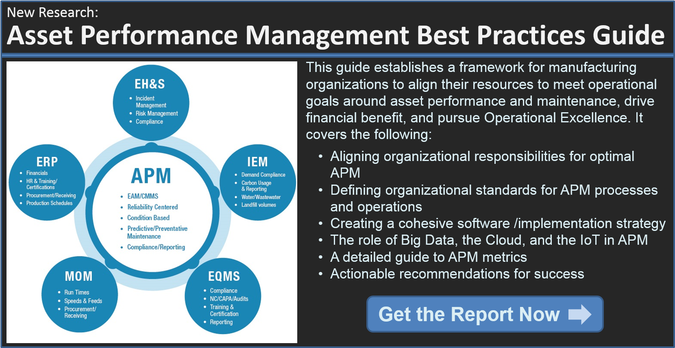