Reliability-centered maintenance (RCM) has been defined in numerous ways over its evolution, from a statistics-based approach, to analyzing equipment failures, to the philosophical or stylistic broader definition more commonly accepted today which espouses a spectrum of styles from reactive maintenance to proactive maintenance with both calendar and condition-based preventative maintenance within those bounds.
Since LNS Research is a firm believer in using data to improve the Operational Excellence of your manufacturing operations, it would seem logical we would tell you the top metrics you need to monitor to improve the performance of your plant if you are pursuing an RCM strategy. However, as I noted in our APM Metrics post, choosing the right metrics isn’t always a cut and dried matter. In that case I made the argument that metrics needed to be role-based. As we look at RCM metrics, I am going to add another dimension to the metrics decision–-that of process.
Not All Manufacturing Plants are Alike
Manufacturing processes are different–-while automobiles and gasoline both are produced in manufacturing processes and both generally considered highly dependent on the other for their usefulness, the way you make them could not be more different. In addition to the vast differences in the equipment used in manufacturing in both plants, robots versus huge distillation columns, the typical refinery operates 24 hours a day every day of the year, while an automobile plant typically runs one or two shifts a day and five days a week. In this case, both the physical process variations as well as the production process variations lead to very different maintenance needs.
Process Versus Discrete Approaches
In a continuous process like refining, which typically operates all day, every day, and for much of the product stream is a single serial line, uptime is a holy grail. If you go down for any reason, production comes to a complete halt and essentially is non recoverable. In situations like this, the emphasis on asset performance is very much centered around detecting imminent failure and preventing it. Condition-based maintenance becomes critical as well as failure modes and effects analysis (FMEA), where you analyze how equipment might fail, what effect that failure might have, and then what steps you can take to prevent that failure from ever occurring. In this type of production environment your RCM focus needs to very much aligned to the uptime goal and those elements which the various FMEA activities you conduct identify as the most critical to achieving that objective. Rather than regurgitate a list of KPIs that are relevant to a continuous-process plant, we'll point you to an article from Maintenance Technology magazine.
In a discrete manufacturing process, like in an automotive or aerospace plant, where there may be significant periods of time available for maintenance activity and merely extending operational capacity for a few hours or days is sufficient maintenance, activities might differ considerably. Also, in many discrete manufacturing operations there are parallel work centers, such as a robot painting operation, where downtime in a single cell only slows but does not stop operation and there are numerous opportunities to recover the lost production through overtime or process reconfiguration. In this environment, KPIs or metrics that measure flexibility and contribute to machine center OEE and maintenance cost-effectiveness might be more relevant than in the continuous-process plant example.
Continuing Down the RCM Path
For those manufacturers just starting down the RCM path, an excellent tutorial on RCM, its evolution, styles, and a comprehensive bibliography can be found here. For those already pursuing RCM or trying to get a broader perspective of metrics, see our Metrics That Matter research.
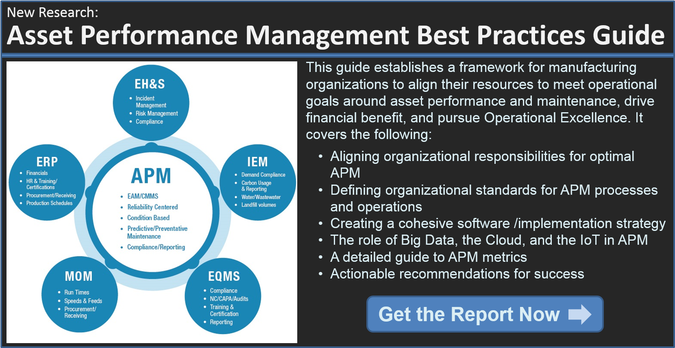