Clinging to existing practices has intensified workforce challenges, forcing the C-suite executives burning platform to focus on human capital. Unfortunately, "The Great Goodbye" continues to negatively impact operational performance with the hemorrhaging of manufacturing talent.%20Initiatives_iStock-858561748.jpg?width=290&height=193&name=Manufacturers%20pursuing%20Future%20of%20Industrial%20Work%20(FOIW)%20Initiatives_iStock-858561748.jpg)
Eighty-seven percent of manufacturers are pursuing Future of Industrial Work (FOIW) initiatives, but only 37% of programs have delivered corporate value. This blog will dissect workforce initiative failure modes and uncover best practices to build manufacturing talent for a future-proof frontline.
Followers Fail with Reactive Focus
Research has identified stark contrast between the nature of frontline workforce business objectives set by FOIW Leaders, the top 19% of companies achieving real success and delivering corporate value through workforce initiatives, and Followers. Leaders tend to focus proactively on business outcomes to future-proof the frontline. In contrast, Followers are significantly more likely to set reactive business objectives such as increased new hire retention and improved safety, quality, and productivity. This is the equivalent of applying bandages to a broken strategy.
Successful organizations don't bandage critical assets across operations, and it's time we see our frontline workforce as one of the most critical industrial assets. Our Industrial Transformation (IX) research found that Leaders ensure IX program heads deeply understand the company's strategy and business objectives.
FOIW Leaders' business objectives provide a valuable lesson to focus on how the frontline will overcome workforce challenges, such as:
-
-
-
Upskilling employees for new ways of working
-
Digitally enable our frontline workforce
-
Improving onboarding speed and knowledge management processes
Manufacturers focused on proactive rather than reactive business objectives can identify and fix the root of the problem and are significantly more likely to create a sustainable, future-ready frontline.
Followers Battle Bridging the Skills Gap
FOIW Leaders aren't just focused on proactive business objectives, but more specifically, objectives target the skilled labor shortage faced by manufacturing. Workforce retirements, an increase in blue-collar mobility, and the lack of applicable skills from next-gen workers are constant battles faced.
LNS Research found that those manufacturers not seeing real success or delivering corporate value are four times less likely to adopt process capabilities to support frontline workforce initiatives. While 38% are working to improve individual skills and competency tracking, a significant gap exists in developing holistic process capabilities for the frontline workforce.
FOIW Leaders are improving onboarding speed, knowledge management processes, and upskilling employees by building process capabilities across the frontline to achieve workforce initiatives. The process capabilities receiving the most focus include:
-
-
-
Work performance and task support (e.g., work instructions and guided procedures)
-
Training and learning management
-
Talent development and career path management
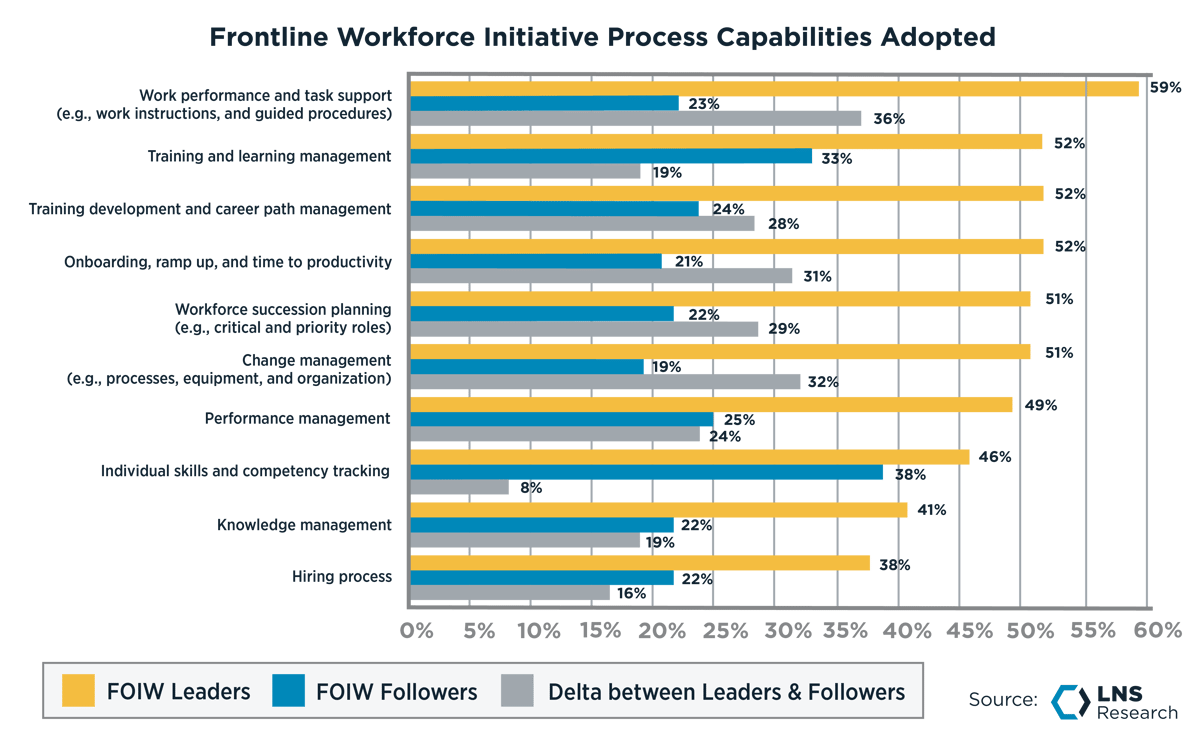
Global Operations Vice Presidents and Heads of Operations must focus on process capabilities to significantly improve the organization's ability to capture and transfer knowledge, leading to increased frontline workforce competency.
Followers' Technology Focus Fails to Improve Employee Experience
Manufacturing has overly focused transformation on technology-driven initiatives. This tactic has left employees overwhelmed rather than feeling more supported. Only 20% of Followers focus on digital technology to support and connect the Frontline Workforce compared to 43% of FOIW Leaders.
Leaders tend to see Digital Transformation initiatives positively impacting the frontline and employee job satisfaction. In contrast, Followers are significantly more likely to see the impact of digital technology reducing headcount. FOIW Leaders are two times more likely to include advanced technology in place to support the workforce and four times more likely to implement human-centric technology designed for the workforce, such as Connected Frontline Workforce (CFW) Applications.
Failing to recognize the importance of digital technology to the next-gen workforce and frontline competency is detrimental to operational performance. Industrial organizations must entice next-gen employees to manufacturing before it's too late. CFW initiatives must focus on providing employees with the proper training, integration across operations, and a user interface that doesn't make you want to slap your mamma.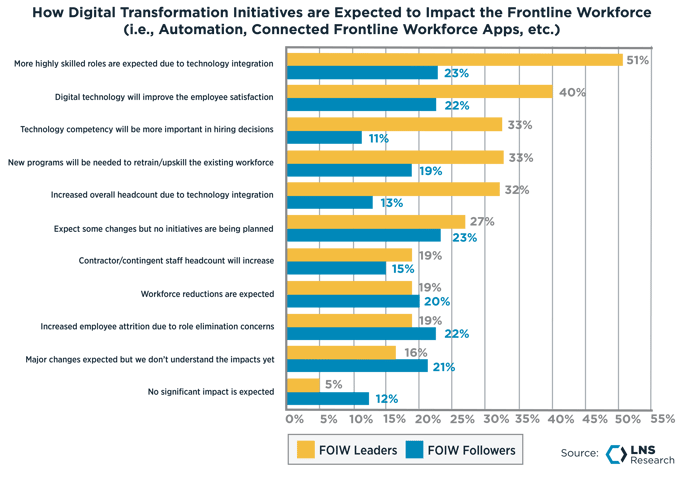
The LNS Research CFW Solutions Selection Matrix assists industrial organizations in identifying vendors offering viable solutions to digitally enable the frontline workforce. Solutions should meet the following basic criteria when considering CFW applications for enterprise deployment:
-
-
-
Product offerings designed for the industrial frontline workforce
-
Leverages digital technology to enable connectivity to and among people, assets, IT/OT systems, and the work environment
-
Established presence in at least one major manufacturing/industrial sector
-
A complete solution proved to provide customers with the vendor's value proposition
-
Functionality that supports a broad range of use cases and flexibility to meet new/changing requirements
FOIW Strategy to Build Manufacturing Talent
Leaders have accepted the need to act and are successfully building manufacturing talent through a proactive and coordinated approach. FOIW initiatives are essential and must be included within the overall IX program. The time is now to develop a FOIW strategy that adapts and transforms frontline workforce operations to empower the workforce.
Global Operations VPs and Heads of Operations who don't learn from failing workforce initiatives are destined to be required to find a new workforce to join.
Stay tuned for more LNS Research insight into the proven strategy FOIW Leaders have found to evolve as the Future of Industrial Work develops and overcomes frontline attraction, hiring, onboarding, and retention challenges.
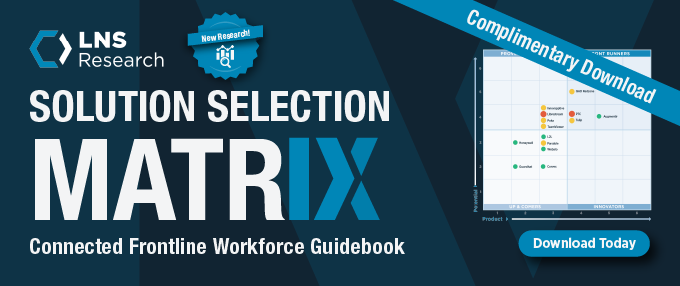