If the adage, “With Change Comes Opportunity” is at all correct, Environment, Health and Safety (EHS) business leaders have opportunity in spades. Entering the second year of the COVID-19 pandemic, change and the ability to adapt to it have become the mantra for industrial organizations to get through the crisis. Over the past year, “resilience” and “agility” were the buzz words of corporate earnings calls and communications, perhaps to the point of overuse regardless of their validity.
One of the major means industrial organizations have relied on to increase operational agility and build resilience is digital transformation. Our COVID-19 research shows that 43% of companies have increased their strategic focus on Industrial Transformation (IX) — the digital transformation of industrial operations — in response to the crisis, while only 18% have decreased IX focus. How does EHS factor in? Among major IX initiatives such as Factory of the Future and Quality 4.0, the digital transformation of EHS management (EHS 4.0) is most likely to have received increased focus and investment.
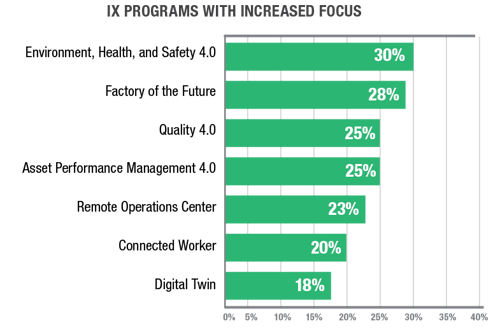
EHS 4.0 Evolves
Several years ago, I wrote on this blog that EHS business leaders had a once-in-a-career opportunity to dramatically advance how the EHS business function adds value to the business. That opportunity was to leverage the macro trend of Industrial Transformation (IX) to help overcome the limits of traditional EHS management and achieve step-change performance improvement.
Around the same time, LNS Research coined the term “EHS 4.0” and published seminal research on the EHS 4.0 Framework as guidance on how industrial organizations can leverage the digital transformation process to improve EHS performance within the context of broader IX initiatives and operational performance. Since then, the concepts of EHS 4.0 have matured and many organizations have started to see success in applying its principles.
As if the challenges of effectively incorporating EHS 4.0 into IX weren’t enough, along came the pandemic. This post presents seven key opportunities every EHS business leader should incorporate into short- and long-term planning in 2021 and beyond. The macro drivers of these opportunities existed pre-pandemic; the crisis has merely served to accelerate and intensify them. This is the time for EHS leaders to decide whether and how to seize these re-invigorated opportunities.
Seven Transformation Opportunities
- Renewed Relevance – The EHS business function has had its challenges over the years in shaking off the old “compliance cop”, cost-center stereotype. The wide-scale disruption of operations that came with the COVID-19 pandemic has created an excellent opportunity to change that perception, as EHS took on a critical role in leading the response. As organizations continue to adapt towards the future, EHS leaders can take advantage of the heightened visibility to become more even more indispensable to the business. This involves delivering strategic value by helping the business build capabilities to be more agile and resilient, especially operational risk management.
- Business Alignment – Our most recent EHS 4.0 survey data shows that organizations with higher EHS capability maturity are much more likely to align their initiatives with enterprise business objectives. The COVID-19 crisis crystallized in the minds of Board members and senior leadership the need for effective EHS and operational risk management systems to safeguard people and operations in the face of change. This is the ideal time for EHS leaders to gain approval of investments that support corporate strategic objectives and enable capabilities needed for resiliency and business continuity such as operational agility, innovation, workforce competency, risk management, and sustainability.
- Strategic Sustainability – One of the richest and most timely opportunities for EHS to align with business objectives is Sustainability, which has undergone a resurgence as a key part of corporate strategy. While not a new trend, it is one that is accelerating in 2021 driven by investor demands regarding disclosure of ESG risks, and increased recognition by a wide range of stakeholders of the certain impact of sustainability issues on an enterprise. In an interconnected world, license to operate, business continuity, stakeholder sentiment, brand value, and ultimately profitable growth are inextricably linked to Sustainability performance.
EHS business leaders can and do have an increasingly big role to play in planning and executing Sustainability business initiatives. Many if not most Sustainability initiatives and metrics are in the realm of traditional EHS management, including people health, safety, and wellness; environmental performance; operational risk; and product and supply chain stewardship. Many organizations place Sustainability responsibilities with the EHS function, creating an opportunity to further align with enterprise business objectives and deliver value.
- Industrial Transformation (IX) – IX is one of the most powerful cross-industry macro trends over the past several years. Most industrial organizations have undertaken IX initiatives (e.g., Factory of the Future, Smart Factory, Connected Operations, etc.), often as the strategic framework to compete and grow profitably. In many cases, Operational Excellence and other continuous improvement programs have been converted to IX programs, or at least closely aligned with them. This creates new opportunities for EHS Leaders to proactively engage in — and even lead — digitalization efforts, using an EHS 4.0 approach to systematically embed operational risk management, sustainability, and compliance and into daily operations.
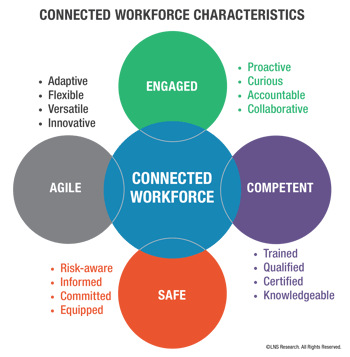
- Connected Workforce – Digitally connecting the frontline industrial workforce is one of the hottest areas of IX investment. Connected Frontline Workforce initiatives had been gaining traction for several years before the COVID-19 pandemic. The crisis accelerated the trend considerably as it demanded new ways of working, safeguarding employees, and ensuring business continuity. Connected Workforce solutions came to the fore to help provide the operational agility needed to adapt to rapidly changing conditions, e.g., to enable physical distancing, remote work, quick upskilling, etc.
Connected Workforce transformation initiatives leverage digital technologies such as mobile devices, augmented reality, sensor-equipped wearables, IIoT systems, and advanced analytics, with the goal of a frontline workforce capable of faster, better decisions; communicating and collaborating more effectively; and executing work with more consistency and quality. EHS business leaders have a prime opportunity to proactively engage in ongoing Connected Frontline Workforce initiatives to implement solutions focused on safety and EHS problems. There is an even bigger opportunity to embed EHS into every Connected Workforce project across operations, including quality inspections, assembly, maintenance, and field service, among many others.
- Data Analytics – The promise of IX is largely based on use of novel methods and tools to collect and analyze operations-related data. Likewise, data analytics is the most powerful and practical means of realizing the promise of EHS 4.0, including real-time risk management. Digitalization of operations is resulting in massive amounts of Big Data from smart connected devices and sensors. This creates the potential for unprecedented visibility into operational risk factors related to assets, people, and the work environment. The challenge is to organize the myriad sources and types of data and convert them into actionable insights to improve EHS and operational performance. Advanced analytics tools and methods including Artificial Intelligence (AI) and Machine Learning (ML) are key to getting this capability.
Most industrial organizations have formal analytics programs as part of their overall IX efforts. EHS business leaders have much to gain by aligning with these initiatives and having a basic working knowledge of data science and governance to collaborate with corporate resources and potentially build data science capabilities within the EHS function. Another high-leverage approach is to co-innovate with the incumbent enterprise EHS software vendor on projects in areas such as predictive, prescriptive, and autonomous risk management.
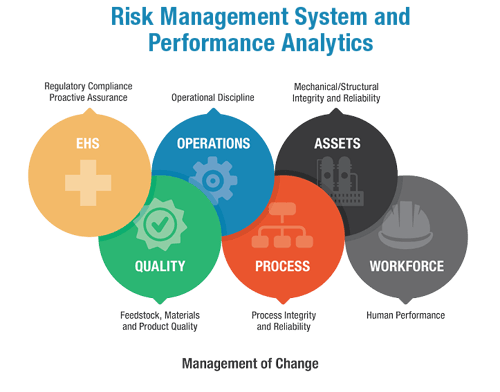
- Operational Convergence – It’s long been a goal to achieve broader and deeper of integration EHS into operations. Our EHS 4.0 research shows this to be a worthy quest. Organizations that have effectively integrated EHS with multiple functions and domains (most notably Production, Maintenance, Quality, and Plant Engineering) report significantly better performance on core operational metrics like profit margin, OEE, throughput, and first pass yield. A core principle of IX is to achieve seamless end-to-end processes, enabling “digital threads” spanning all relevant functions, sub-processes, and teams. Optimization requires that EHS compliance obligations, risks, and opportunities be embedded into enterprise and operations-wide transformation efforts.
IX and its enabling digital technologies give EHS business leaders a much better toolbox for breaking down organizational silos and driving cross-functional process improvement. But the real breakthrough with IX is vertical integration of business processes, systems, and data (IT) with manufacturing technology, automation, and control systems (OT). Increased collaboration between the formerly disparate worlds of IT and OT, and the application of advanced analytics to combined Big Data facilitates true Operational Convergence, of which EHS should be a key part.
Onwards and Upwards
At the risk of sounding hyperbolic, it’s fair to say that EHS business leaders now have not one but two “once-in-a-career” opportunities to impact industries, organizations, people, and their own careers. How lucky can you get? The first is to incorporate an EHS 4.0 approach into their organization’s IX digital initiatives. The second is to leverage the COVID-19 crisis to innovate for long-term benefits. This could entail taking advantage of increased mindshare, better collaboration, more resources, emerging technologies, and increased executive commitment, among others. Although the pandemic has brought disruption, headaches, and harm, it's also created or accelerated opportunities for leadership and the rapid evolution EHS management as a business function and profession. EHS business leaders are positioned better than ever to be agents of change. Opportunity knocks.
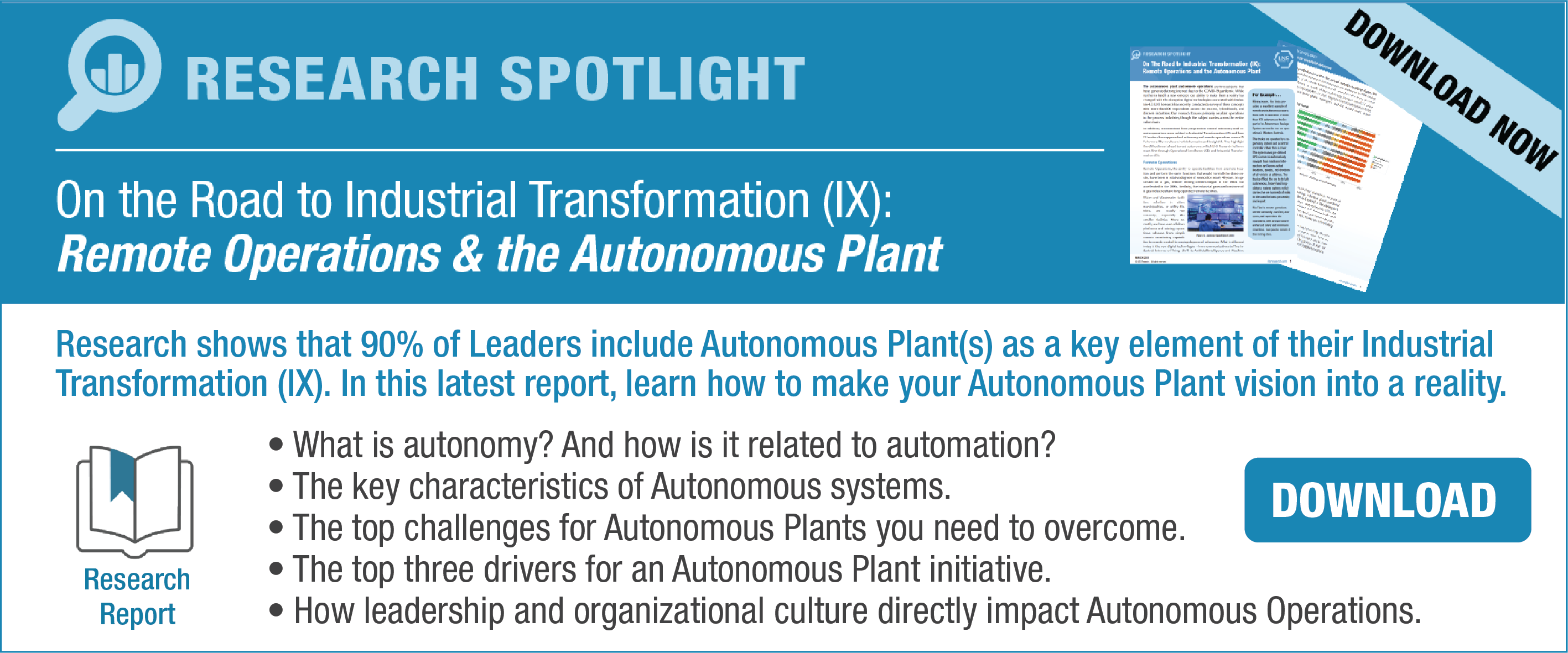