Quality organizations generally have a tough time tracking metrics. Inability to effectively track metrics consistently ranks in the top three challenges facing quality leaders. However, Total Cost of Quality (TCOQ) is more than just another quality metric. The Top Strategic Objective in quality is to reduce TCoQ, outranking other notable objectives such as “improve customer experience,” and “ensure compliance.” Surely, we do a better job with TCOQ than with other metrics?
Click here to speak to Dan
If TCoQ Isn’t Effectively Measured, How Can We Reduce It?
Unfortunately, this isn’t the case. The graphic shows the quality metrics that respondents claim to track, and TCoQ is #2 on that list! Looks promising at first, but let’s dig deeper.
LNS’s Quality Management survey tracks Cost of Quality using ASQ’s TCoQ definition, which is the most common in use. In this definition, TCoQ is the sum of Cost of Poor Quality (CoPQ) and Cost of Good Quality (CoGQ). CoPQ is further decomposed into CoPQ-Internal and CoPQ-External, and CoGQ is broken into CoGQ-Appraisal and CoGQ-Prevention.
In the survey, every respondent that says they track TCoQ is asked for current TCoQ performance, using ASQ’s definition. This is where the wheels come off - 44% respond that they “Don’t Know.” Therefore, just 17% of quality leaders know current performance in TCoQ. This passes the sniff test – CoQ is often very difficult to measure and even fewer than the 17% can likely use TCoQ to make decisions about quality Operational Excellence.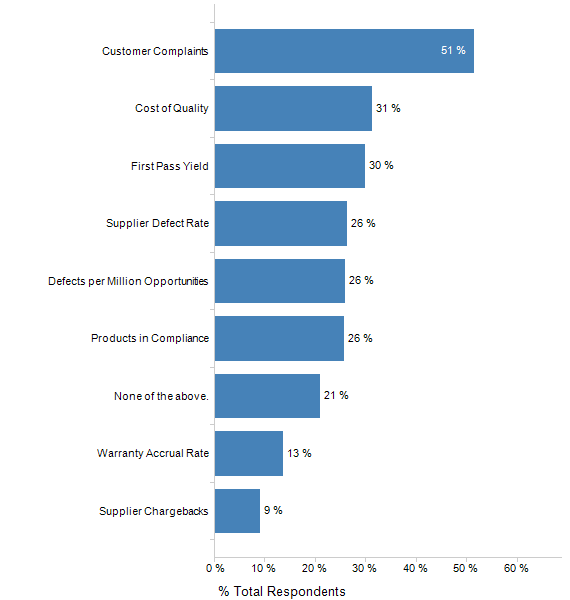
Lack of TCoQ Data Compromises the Business Case for Quality
We’ve just uncovered that industry cannot effectively meet its top strategic quality objective. How then can this metric be practically used to build the business case for quality? Simple - it can’t. We talked with many quality leaders about LNS’s research into the executive business case for quality, and they told us that while leaders aspire to use TCoQ for investment justification, they lack both current TCoQ performance data as well as a TCoQ cost breakdown structure that would allow the TCoQ to be used to drive investment.
Additionally, companies looking to measure TCoQ using the ASQ definition are often unable to come to a practical method to split costs between CoPQ and CoGQ elements. For instance, how should labor costs be divided when the same employee works on both Good Quality and Poor Quality activities? The same quandary exists for capital equipment. While it is possible to divide these costs, it requires extensive record-keeping which reduces agility and consumes resources.
Companies need a TCoQ definition that can be practically implemented, easily managed and effectively leveraged to drive Operational Excellence decisions.
An Alternative Definition of TCoQ
In an effort to make this important tool more usable, here is an alternative definition:
Total Cost of Quality (TCoQ) = Planned Cost of Quality + Unplanned Cost of Quality
Planned Cost of Quality = “Quality budget.” Like a budget, it includes planned capital expenditures as well as operational expenditures, and is reviewed annually. The budget should include the quality department personnel as well as equipment used by quality, without having to break these out by their intended use.
This should not include quality costs incurred by other functions in performance of quality activities, as this will increase effort to deploy and manage. Does quality need to “pay” development to perform an FMEA? Should quality pay services to replace a failed part? Recall that quality should be a responsibility, not a department. As a general rule, adding cross-functional costs into the Planned Cost of Quality will overcomplicate the TCoQ.
Unplanned Cost of Quality = “everything that isn’t planned”. This includes costs incurred to address quality failures and events, as well as unplanned investment in new resources. Examples include costs associated with scrap, rework, corrective actions and recalls. Of course, these costs can be projected, but they should not be included in the Planned Cost of Quality because they are not planned.
This is where a company should consider the labor costs that came from unplanned cross-functional engagement. Other departments should effectively send a “bill” to quality for these unplanned activities. In order to aid reporting and Operational Excellence decision-making, the next tier of the cost breakdown structure could follow the corporate Operational Architecture.
Find a Definition for TCoQ and Use It
Regardless of which definition is used, companies should find a definition for TCoQ that is easy to deploy, easy to administrate, leads to effective decision-making. Done properly, TCoQ can be a great tool to drive continuous improvement and profitability.
NEW eBook is a must for Quality leaders! This eBook provides senior leaders with best practices for building a business case around quality and the foundational framework needed to gain executive commitment.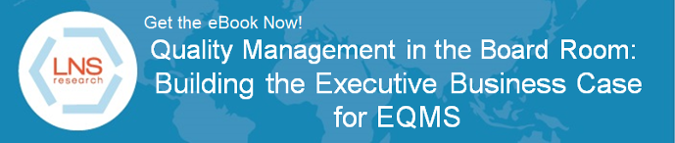