Seventh Life of MOM - Refined
Almost four years ago, I wrote about the "7 lives of MOM," a vision into the future of MOM architecture, and how it would be deployed. The 7th life was defined as “No MOM,” where the functionality previously implemented in MOM systems would be distributed as apps across an Industrial IOT (IIoT) platform. This still seems like a good idea to most and the reality is getting closer, but in a different environment than that we had envisioned.
LNS’ research on Industrial Transformation (IX) platforms demonstrates that the operational, and in particular data, architecture required to support IX is large and complex. We have defined the IX platform that is the base for transformation and the sophistication required to become an IX Leader. However, there are thousands of smaller manufacturers who are starting from a situation much less sophisticated. Many have basic paper-based production management and reporting, and they also have some traditional continuous improvement (CI) processes such as Lean.
The jump from manual to automated invariably needs top management approval and takes many years of hard work by influential manufacturing leaders to persuade the executive team to take the plunge. One common roadblock is the “not another ERP” syndrome that inflicts many manufacturers who have overspent on ERP with slower than expected returns. However, today is a good time to be discussing investing in manufacturing as the advent of programs such as Smart Manufacturing and Industrie 4.0 has brought to the fore the benefits of investing in manufacturing. Indeed, the COVID-19 crisis and the supply chain disruptions it has exacerbated are leading manufacturers to do something!
Once committed, the returns of data connectivity can be fast and continuous if a realistic approach is taken.
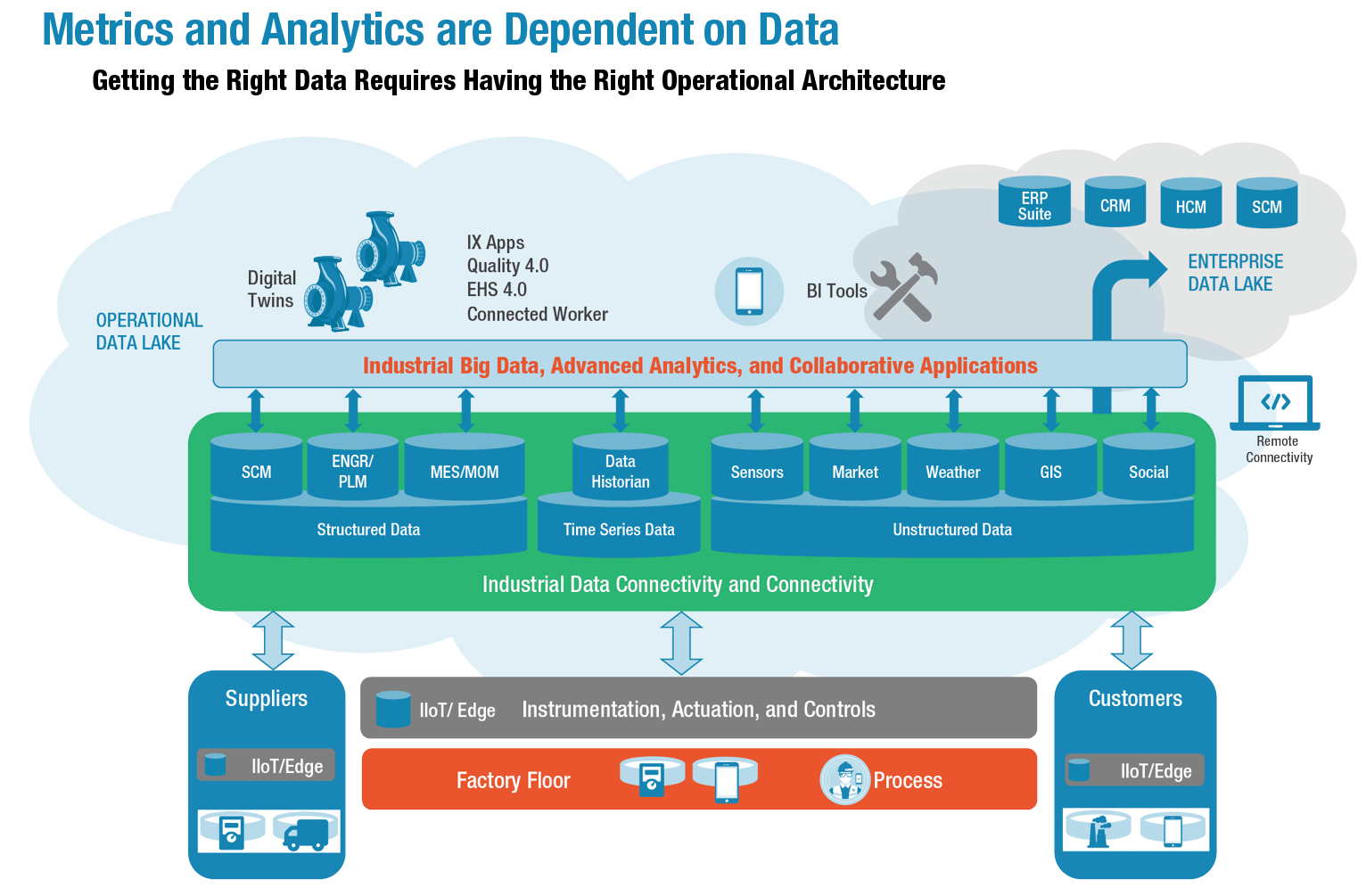
Do not do this! This architecture tries to depict an end state for a large and sophisticated enterprise with tens to hundreds of plants and an integrated global approach. Instead, do two things:
- Choose an MES system that can be installed with few functions but solid data connectivity. Be aware that big MES is not the same as small MES.
- Find simple Industrial Internet of Things (IIOT) devices that will allow you to connect your standalone machines.
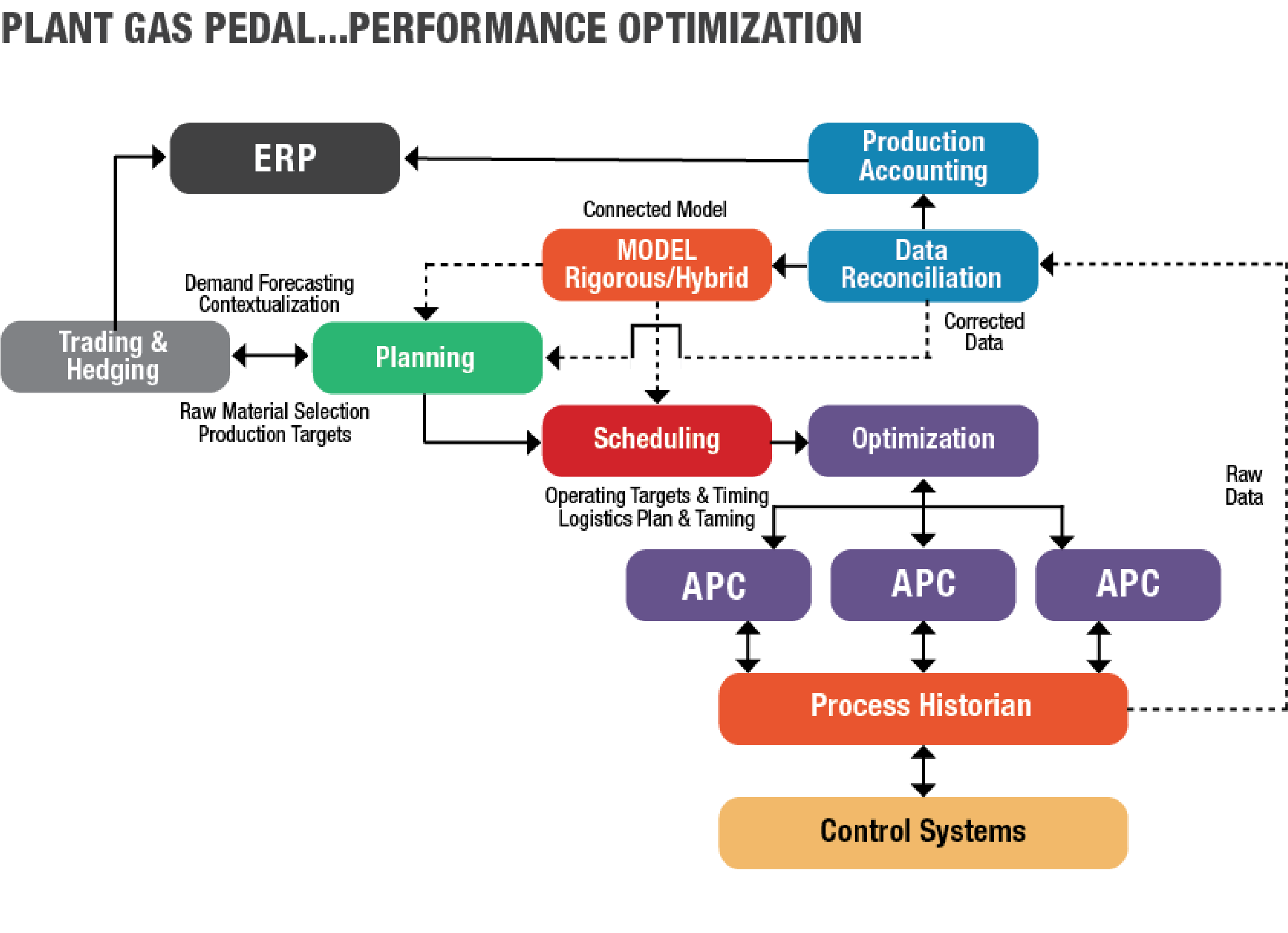
Connect and Go
Perhaps you have some older machines that are manually operated and monitored. It is very likely that they have internal data that can be accessed with simple input and output connections. By bringing the data into MES and simple monitoring screens, you will, for example, immediately benefit by being able to measure cycle times. Without more, the value that an operator and his managers can achieve is measurable. Once you start to use the power of your MES, the possibilities are endless.
Minimal infrastructure for communications and connection to multiple machines can quickly lead to a solution that allows office-bound supervisors direct access to all of the machines. Many MES systems have easy-to configure performance and quality applications that allow non-expert users to build their own screens for simple tasks. Those that support the much more sophisticated “Low code/ No code” programming environments are unquestionably interesting but probably beyond the current scope of those starting off on a simple digital factory.
In most of the manufacturers that are considering their first plant level integration, basic business systems, especially ERP, are probably one of the fastest returns available to connect the plant to the ERP. Nothing complex is required – just replace the paper (and excel) processes that were used to get orders to machines and results back to the business. Once information is available where and when it is needed, everything will change.
IT and OT Support
Many large manufacturers talk of information technology and operational technology (IT/OT) convergence as a pre-requisite for Industrial Transformation but the needs are more fundamental for the new digital factory: IT and OT getting to understand each other from a cultural and technological view should be a key goal. Successfully setting common goals and cross support for the infrastructure will greatly improve your chances of success.
You Are Not Alone
Talking with vendors in the smaller MES market, LNS Research has found that factory connectivity is booming. Manufacturers are, as we said above, realizing they have to do something with manufacturing. To get the best chance of success, talk to both potential MES vendors and also to your peers in similar manufacturing industries. You will surely find many companies in the same predicament – how do we get started? It is not difficult nor expensive but it does need long-term executive commitment. Start now and carefully manage the progress to ensure continuous improvement.
MES vendors should not rest on their laurels. SME manufacturers want a simple solution that combines connectivity, data collection, and basic operations. It should be easy to install and need only a few weeks for an initial project. In upcoming blogs, we will revisit the 7 lives of MOM and address the different needs of smaller and more complex manufacturers. For now, MES vendors should consider how to offer a simple solution that satisfies a wider MES audience.
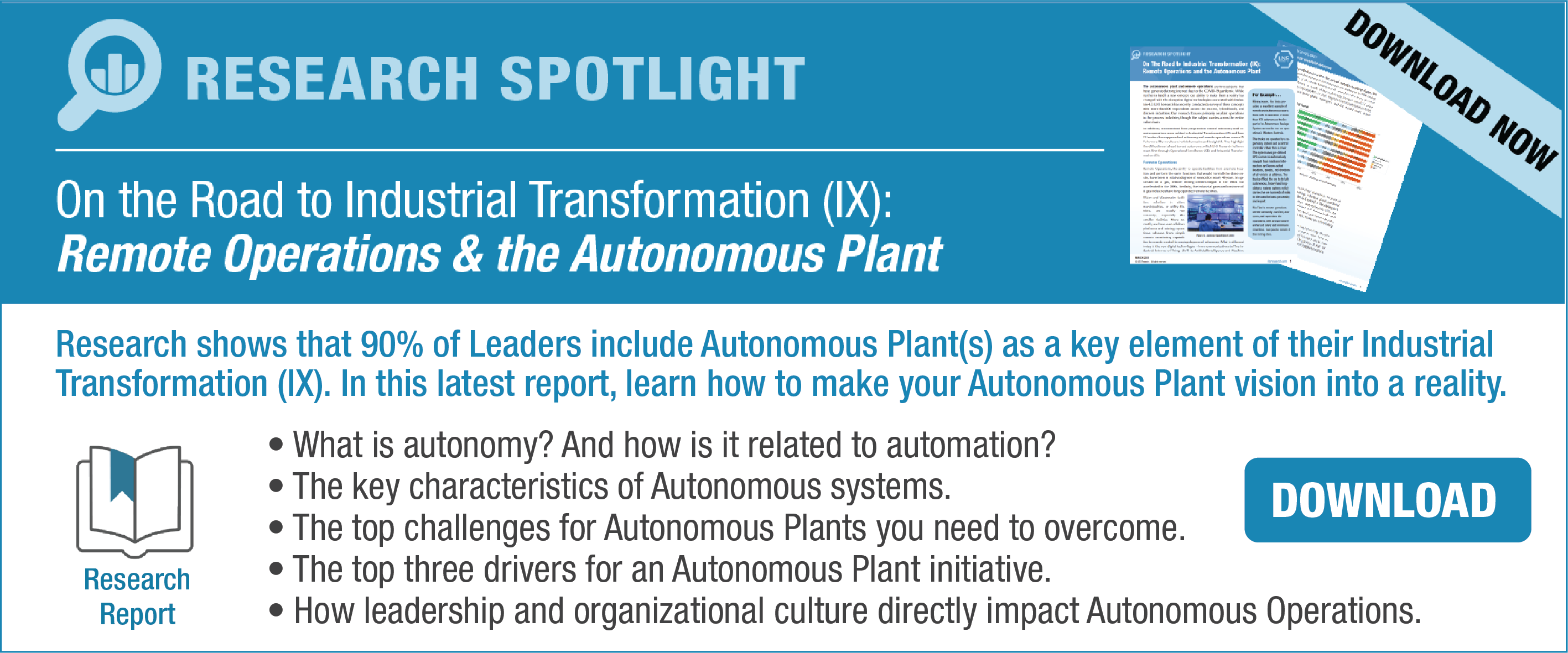