Every day there is another story or sign that there might be an economic downturn in our future. When we look away from the news, we see a different reality. Manufacturers are struggling to keep up with demand and fulfill orders. We hear from many of our member end-user clients that they are having trouble finding and keeping people to maintain their operations. Forecasts don’t project a downturn in demand.
What should we believe? Are the news stories a self-fulfilling prophecy or a harbinger of hard times ahead? How do we reconcile the present, where we are scrambling and struggling to keep up with pent-up demand and seemingly random supply chain outages, with a possible future where we are struggling to keep the lights on and forced to make tough choices about who to retain?
LNS Research has conducted some new research recently on just these sorts of questions. We conducted this research over the late summer months of 2022. One caveat is that economic sentiments and realities can change very quickly, and what we saw in late summer may not be the situation on the ground this fall or winter.
Economic Uncertainty is Uncertain
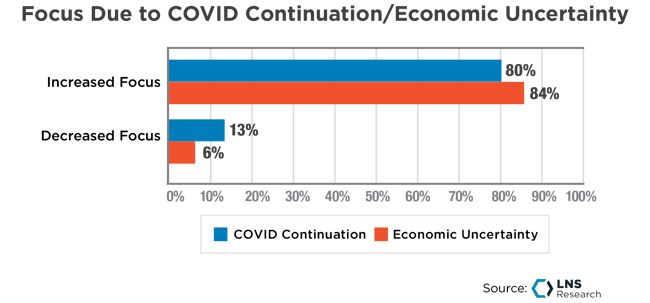
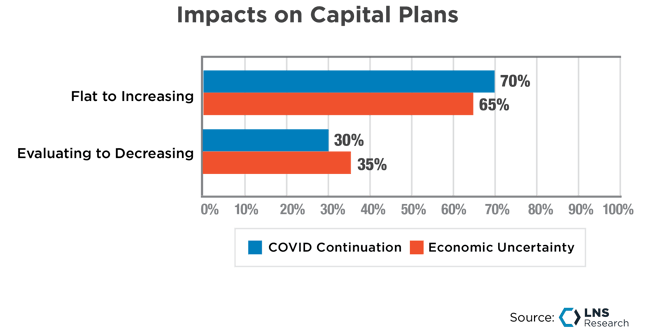
Not Changing course on Transformation
In late summer the overall view on possible economic uncertainty was overwhelmingly that we don’t see it happening. At a macro level, there are no signs of forecasted demand decreasing, nor are there signs of pulling back on spending. See the caveat above. This sentiment can change very rapidly but that’s the story in manufacturing today.
There are a few strong themes that came out of this research that Quality leaders need to pay attention to and prepare for, regardless of if they believe there is a downturn headed our way or not.
Those themes are:
-
-
-
Agility
-
Flexibility
-
Consistency
Agility is a many-faceted concern for manufacturers. The concept of agility spans from the supply chain to product design, and customer expectations.
For the Quality leader, agility in the supply chain looks like rapidly pre-qualifying additional new potential suppliers ahead of a supply chain crunch. The Quality leader can enable organizational agility by being proactive in both new supplier qualification activities, and collaboration with existing suppliers.
Agility in product design looks different by industry but generally is focused on resizing, redesigning packaging, and preparing inspection devices and/or people for the changes so that there is no interruption as resized or repackaged product moves through the inspection and approval process for release.
Agility in manufacturing support looks like rapidly shifting priorities for manufactured products because demand shifts rapidly.
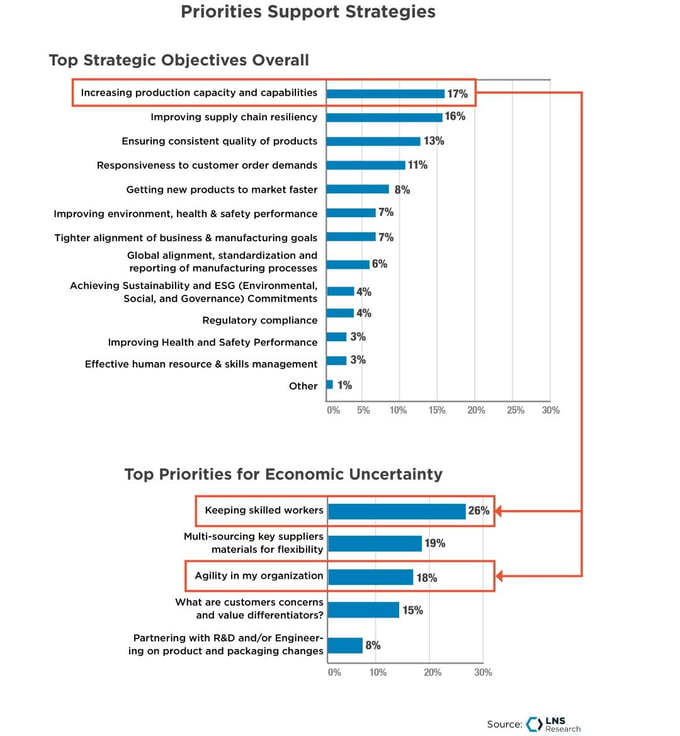
Strategies and Priorities Align
A key role that most Quality organizations play in making this possible is to ensure the workforce is cross-trained and qualified to run a variety of processes, enabling operations to rapidly shift demand around in response to sudden customer changes.
Agility in customer-facing processes centers around leveraging the Digital Voice of the Customer/Consumer to gain early insights into consumer value differentiators and turning those into a competitive advantage, gaining more of a shrinking share in the dogfight of an economic downturn.
Product agility is also recipe/product design change. Quality leaders must develop a risk-based proactive approach to stay ahead of unforeseen failures these changes could create.
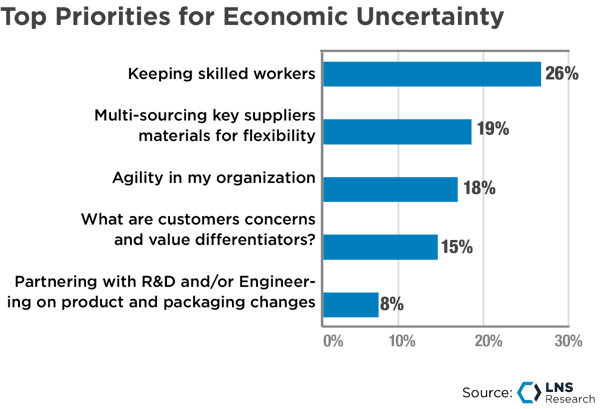
Agility and Flexibility are Top of Mind
Flexibility is a close cousin of agility and the child of preparation. For instance, manufacturing operations cannot be flexible in production sequencing if the labor force is not adequately qualified to handle that shift by being sufficiently cross-trained to be able to respond to the change. Connected Frontline Workforce (CFW) applications can help here.
Supply leaders can’t shift from Supplier A to Supplier B if there is no pre-qualified Supplier B to move to when Supplier A has an issue. The top strategy for managing supplier risk is to multi-source materials.
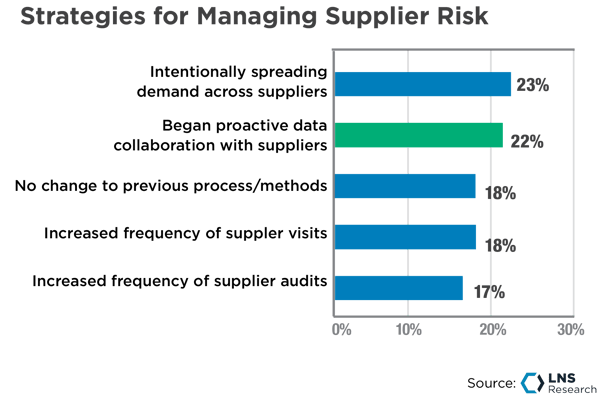
Tighter Data Collaboration is a Top Strategy
Our research shows that the second leading strategy for managing supplier risk is to collaborate using data with the supply chain.
Quality leaders have a crucial role here to leverage analytics into the supply chain and collaborate robustly with suppliers to head off, or at least give an early warning of supplier issues on the horizon.
This imperative aligns with our previous research that shows that Quality 4.0 leaders are more than three times as likely to be pushing Prescriptive Analytics into their supplier chains than followers.
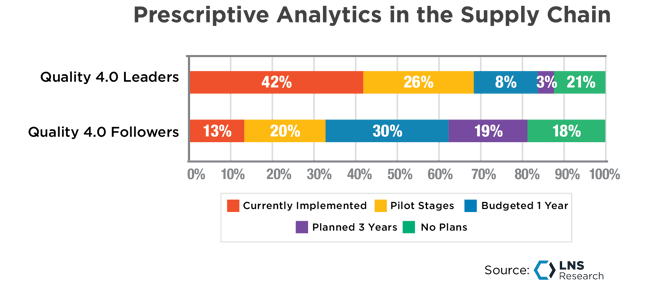
Quality 4.0 Leaders are three times more likely to push Prescriptive Analytics into the Supply Chain
Consistency is something that everyone with Quality or Performance Excellence in their title understands:
-
-
-
Consistency in customer/consumer-facing delivery activities
-
Consistency in product design and manufacturing
-
Consistency in supplied material
These are and have been top areas of concern for Quality and Performance Excellence professionals for decades. Reducing variation is the main aim of a Six Sigma project. The challenge in the new future of economic uncertainty is to maintain consistency in the face of increased agility and flexibility in manufacturing operations. Consistency is challenging in good times; it will be exponentially more difficult when acting with agility and flexibility to deal with supplier issues and the shifting sands of customer/consumer demands.
Our research on Economic Uncertainty shows a potential new use case for the Digital Voice of the Customer to support a top priority for understanding shifting customer/consumer preferences and value differentiators.
Digital Voice of the Customer (DVoC) tools can deliver insights into the company that can be leveraged into risk assessments for anticipated product changes, new product designs, or existing product enhancements to improve the customer/consumer value perception, even in the face of resized, and reconfigured package sizes and potential price increases.
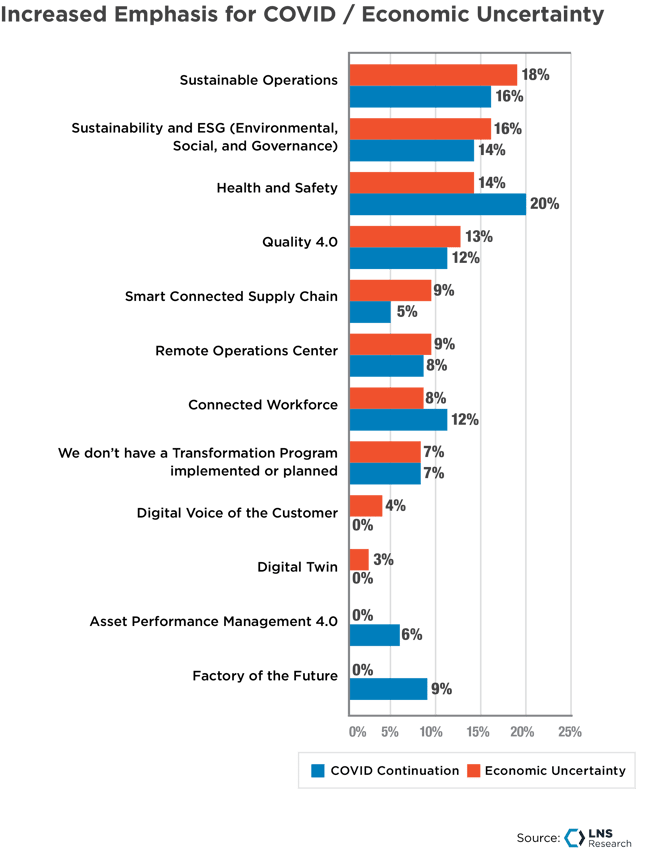
Digital Voice of the Customer to gain insight into Value Enhancement
A key ally for the Quality leader in the pursuit of Agility, Flexibility, and Consistency is the deployment of Connected Workforce applications to frontline workers. Those who are the first to see and respond to issues should be armed with the information they need to make effective decisions consistently while pivoting left and right to maintain productive operations in the face of supply chain issues and shifting demand. Connected Frontline Workforce applications can also help shorten the learning curve for new associates, getting them to the level of proficiency of someone with years of experience in mere months.
This is the charter of the Quality leader, to act with agility and preparation to enable agility and flexibility in the partner organizations when it’s necessary. Quality teams also need to adopt an agile, flexible mindset to help find the win-win scenario that keeps the company moving forward in rough seas.
We are in a period somewhat unique in economic history. At once dealing with unprecedented pent-up demand released by the abatement of COVID-19’s worst period (the “Great Resignation”), workforce migration to better, more meaningful, and balanced work (the beginnings of the “Great Retirement” of Baby Boomers and Gen-X’ers), and the dark clouds on the horizon for a possible economic downturn. Navigating these uncharted waters will require agility, flexibility, and overall, consistency to successfully come out the other side.
Recommendations for Quality Leaders to prepare for Economic Uncertainty:
-
-
-
Develop a laser focus on risk. Achieving maximum agility and flexibility requires keeping your finger on the pulse of multiple possible failure points, all at once. This requires a mindset shift from reactive to proactive approaches focused on risk identification and mitigation.
-
Embrace Data and Analytics. A clear signal for managing risk in the supply chain is embracing data-based collaboration with suppliers. That coupled with previous research that shows that Quality 4.0 Leaders are three times more likely to be pushing Predictive Analytics into the supply chain sends a clear message to Quality leaders to engage with suppliers on a data basis to avoid being caught flat-footed by a supply chain issue.
-
Leverage the Digital Voice of the Customer. DVoC applications have the potential to gather insights about customer/consumer preferences and value differentiators, a top four priority for economic uncertainty. These insights can be leveraged into NPI and product revision activities to gain a competitive advantage over competitors who don’t pay attention to this source of insights.
-
The path to Agility and Flexibility in manufacturing is through Connected Frontline Workforce (CFW) applications. As we move closer and closer to the generational shift in the workforce associated with the coming “Great Retirement” of Baby Boomers and Gen-X’er, the next experience gap will be bridged by Connecting the Worker to digital intelligence. CFW is the best friend of the Quality leader in giving the frontline worker access to the tools needed to make good decisions in the moment.
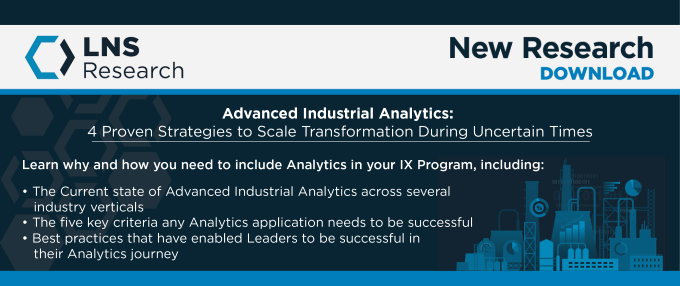
All entries in this Industrial Transformation blog represent the opinions of the authors based on their industry experience and their view of the information collected using the methods described in our Research Integrity. All product and company names are trademarks™ or registered® trademarks of their respective holders. Use of them does not imply any affiliation with or endorsement by them.