We have written about some of the woes for Quality 4.0 Transformation programs here in the past, such as Quality:
-
-
-
Being seen as a policing function
-
Having goals that are misaligned with organizational goals
-
Operating with shoestring budgets
-
Needing to focus on reducing the cost of the Quality Function
-
Being too focused on compliance
I could go on. In our most recent research on Quality 4.0 from 2021, we asked a question about things Quality 4.0 leaders had a deep understanding of. The company’s strategic objectives were at the bottom of that list for Leaders and Followers. This stands in stark contrast to similar research on Industrial Transformation (IX) Leaders’ deep understanding. Their understanding of the company’s strategic objectives was the second-highest response.
What is really going on here, though? If we look at results as an indicator of success or failure, we get a different picture. Quality 4.0 Leaders are orders of magnitude more likely to achieve improvements in business KPIs than Followers. On average, they are over 70% (!) more likely to produce double-digit improvement from their Quality 4.0 Programs! (Figure 1)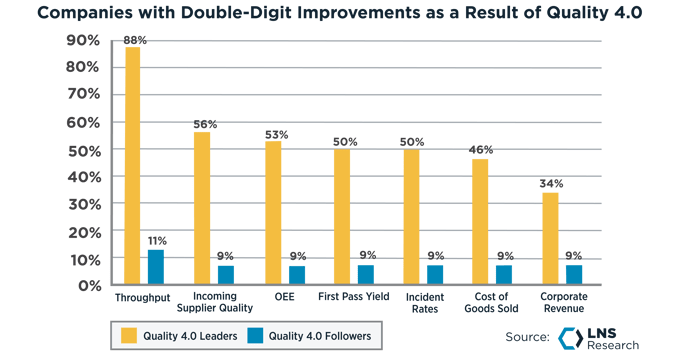
Figure 1: Quality 4.0 Leaders get results!
How does this compare with Industrial Transformation overall? In our Industrial Transformation Readiness research from 2021, we asked about Revenue, Operating Margin, and Cost of Goods Sold (COGS), and some significant improvement was also seen there. Two programs with two different sets of leader traits, both getting considerable business improvement.
One additional detail might help explain.
Quality is the major sub-initiative of overall Industrial Transformation programs, so some cross-pollination occurs. (Figure 2)%20Team.png?width=624&height=575&name=Representation%20on%20an%20Industrial%20Transformation%20(IX)%20Team.png)
Figure 2: Quality is the Top Contributor on an IX Team
The conventional wisdom would be that a leader with deep Quality domain expertise would be best to lead a Quality 4.0 program. However, that may not be the case. When we look at what it takes to lead a successful transformation program, there are significant parts of the role that Quality leaders are perhaps not best prepared to do.
In most industrial organizations today and for the past 90 years, Quality has not been its own independent function within the business. It’s typically nestled within Engineering, Operations, R&D, or Supply Chain. Despite the ever-present lamentations for independence, Quality as an organizational unit is not independent, and the trend is moving away from independence. Quality is typically a sub-function of a broader organization-wide function, fulfilling a critical aspect of the organization’s mission. Is it really realistic to think that a Quality Leader will suddenly be able to take on these broad organization-wide challenges when nothing in their prior experience has prepared them for those things?
This includes organization-wide challenges like:
-
-
-
Building a rationalized budget. One of our LNS Research Best Practices for transformation readiness is to budget sufficiently for the effort to progress smoothly. Some Quality Leaders don’t have P&L Budget experience or responsibility, making this a challenging ask for most career Quality Leaders.
-
Collaborating with other functions. Our research on Quality 4.0 shows that successful program leaders engage in a high degree of collaborative and partnering behaviors. In the day-to-day execution of the Quality mission, the main partner relationship is an adversarial relationship with manufacturing. Most Quality Leaders don’t “grow up” learning how to seek out a win-win scenario; they are used to having to take principled stands.
-
Speaking the language of business. See reference to principled stands above. Most Quality Leaders are used to having to defend their decisions on the basis of customer sentiment and doomsday “what-if” scenarios about recalls, lost sales, etc. These tactics make Quality the function that cries wolf. It is rare for a Quality Leader to put issues in the context that most partners would understand, dollars and cents.
-
Communicating and motivating at the organizational level. Most career Quality Leaders don’t operate at the organizational level. Quality doesn’t own a mission-critical chuck of the purpose for the business’s existence. It is rare for a Quality Leader to be a legitimate C-suite executive, even most of those titled as Chief Quality Officer are at least one level removed from the CEO. As a result, most don’t get to practice organization-wide communication and motivation, a skill set that is critical to success in Quality 4.0 transformation, as it is in overall Industrial Transformation.
To expect a career-Quality Leader without the benefit of intentional development to suddenly rise to the occasion is probably asking too much.
All of this would explain why our research shows that 80% of Quality 4.0 transformations are NOT led by the Quality Leader; they just aren’t equipped with the tools needed to do the job.
I mentioned above that a Quality 4.0 transformation is the top sub-initiative of a broader IX program. Supporting this important effort, IX Team membership is topped out by Quality representation in IX Leader companies. (Figure 3)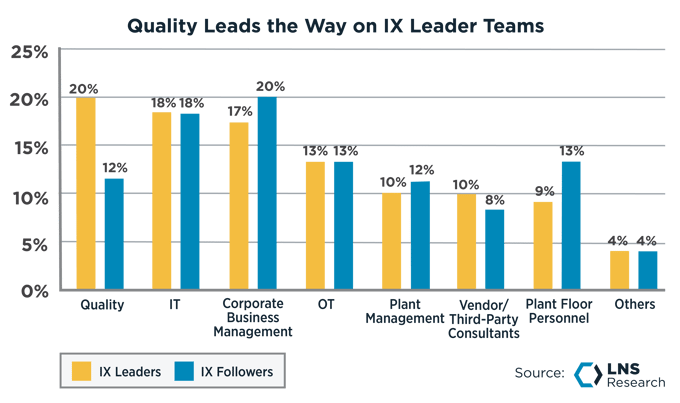
Figure 3: Quality is the Top Contributor for IX Leaders
So then, the good news here is that among IX Leaders with a Quality 4.0 transformation as a sub-initiative, those with deep domain experience in Quality participate in setting the direction.
For Quality 4.0 transformations to break the cycle of an outside-in approach and reduce the cost of the Quality functions scope, they must be led by someone who understands the organizational purpose of the Quality function but also:
-
-
-
Understand how the business functions
-
Communicate at the top level of the organization
-
Motivate and create alignment through that communication
-
Understand the value of collaboration and partnership, and know how to do it
-
Understand and communicate in the language of business
The answer might be a hybrid leader of the type that exists in some organizations, where a “well-rounded” leader is valued and built with intention through organizational rotations or other tactics focused on creating leaders with an intentionally broad organizational experience.
Quality Leaders who aspire to lead Quality 4.0 Transformation initiatives should:
-
-
-
Get out of the core Quality function and experience other parts of the organization. There are a few good places to get the experience needed to effectively lead a transformation, such as:
-
-
If the company has a Project Management Office (PMO) function, this is a great place to gain the needed experience in managing long-term project communication, marshaling of resources, and budgeting.
-
Get involved in the company’s Continuous Improvement (CI) program. Leading CI projects is a great way to gain necessary presentation, data-based decision-making, project management, and change management skills.
-
Volunteer for a job rotation program if one exists in your organization.
-
Volunteer for corporate programs that expose you to employees and leaders outside of the Quality function. This builds your stature in the company and makes you a “known entity” to leadership.
-
Learn the goal-setting and budgeting processes at your company. Misalignment of Quality goals to business goals is a top disconnect in Quality 4.0 programs, and Quality 4.0 programs are notoriously underfunded.
-
Go to school on the technology that could potentially impact a Quality 4.0 transformation. Right now, these include:
-
-
-
-
-
Vision cameras
-
Advanced Industrial Analytics
-
Robotic Process Automation (RPA)
-
Machine Learning/Artificial Intelligence
When we refresh the Quality 4.0 research next year, we will be exploring this topic in great detail to learn if this is, in fact, true in Quality 4.0 leader organizations today. Keep an eye out for more research coming soon.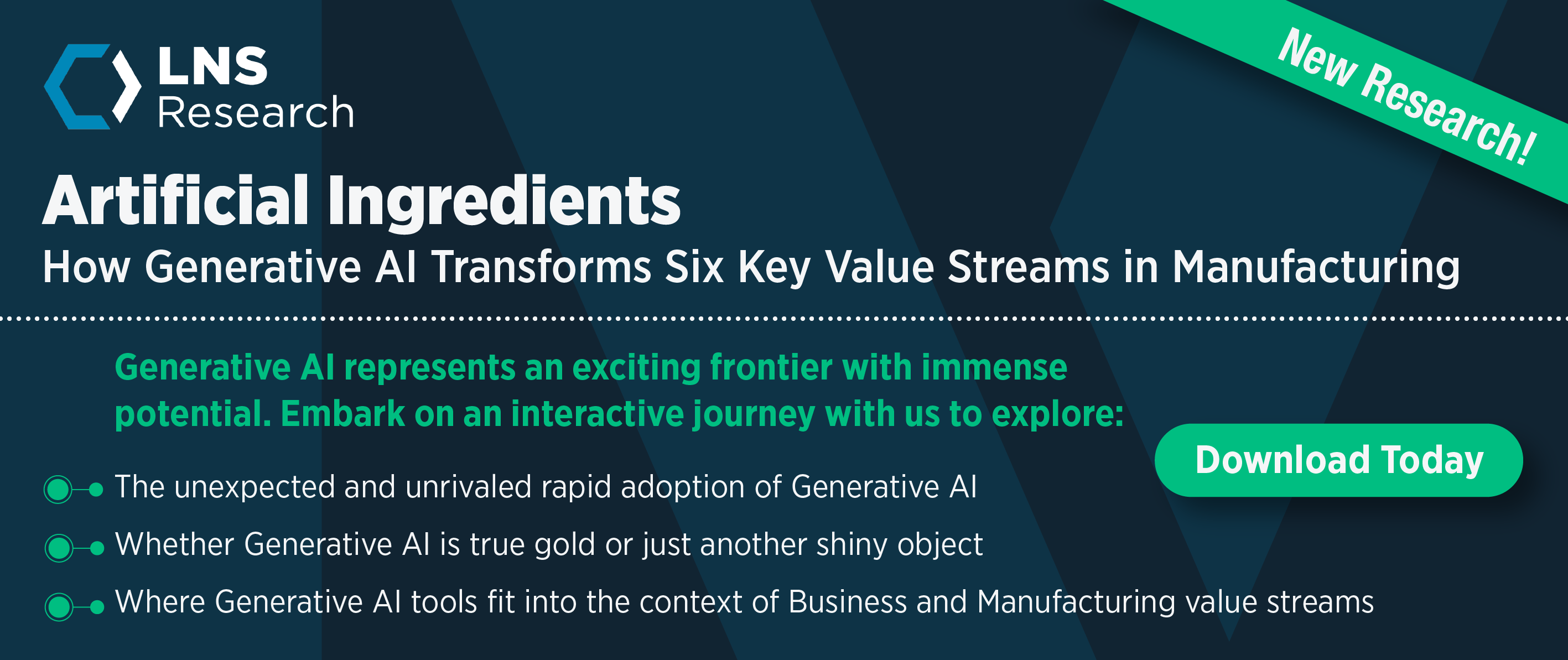