Today's manufacturing workforce looks radically different compared to 2019. Gone are the 30-year veterans with average tenure down to only three years in 2023. To make matters worse, 50% of new employees leave manufacturing roles within the first 90 days.
Traditional approaches to achieving a trained and competent workforce are failing. New generations demand step-change improvements across safety, health, and sustainability performance. Industrial organizations must fundamentally evolve to
meet the needs of today and the future.
The only way for manufacturers to face dramatically increased risk with a less experienced workforce is to focus on improving onboarding and training. In this blog, we will explore the top three capabilities that accelerate employee onboarding and enable the 30-day employee to achieve 30-year performance.
Accepting the New Reality
Operations' attitude toward "we always find a way to make it happen," and the "can-do" response is a deeply rooted concept that runs through the heart of manufacturing. Many are still clinging desperately to the hope for the pre-pandemic workforce and performance to return. Unfortunately, declining workforce tenure, a shrunken labor pool, and the skills gap will only worsen.
"The Great Goodbye," as we call it, is upon us. The last of the baby boomers are retiring, Gen X is entering retirement age, and Gen Y and Z turnover accelerates as many now prefer a job over a career. Ten percent of today's employees will be gone for good over the next three to five years, taking their knowledge with them. The impacts we are seeing on safety, quality, and productivity performance are only the tip of the iceberg.
Most industrials are making surface-level changes such as adjusting pay, providing wellness programs, and offering flexible work to improve frontline operations. These actions are costly and ineffective, proving manufacturers can't pay their way out of this situation. There is an urgent need to improve onboarding or experience a future of firefighting to survive.
Not all manufacturers are struggling. Leaders have already accepted the new reality and are performing 55% better, on average, across key operational performance indicators. Their secret has been in the capabilities that were first adopted and then matured to enable newer generations.
Identifying the Capabilities to Invest In
Millennials and Gen Z employees are projected to comprise 64% of the workforce by 2031. Sixty-one percent of industrials find that newer employees lack the skills to collaborate effectively. Leaders foresaw catastrophic impacts unless transformational changes were made to attract, train, and retain this newer generation.
As a result, Leaders have directed their focus to getting a 30-day employee closer to a 30-year performance level sooner without sacrificing safety or quality by setting proactive business objectives to upskill employees and appeal to the new generation. The top three capabilities we found Leaders investing in to enable success are:
-
-
-
Knowledge Management
-
Connected Frontline Workforce (CFW)
-
Virtual Operations Center
Let's examine why these capabilities have enabled Leaders to evolve fundamentally and how others can leverage these learnings to transform frontline operations.
Bridging the Skills Gap
Today's processes, work instructions, and even training materials are often written for a much more experienced employee. With the 30-year tenure having been the norm, it's typically not even recognized. Newer employees coming in have a very different skillset and the luxury of still getting trained by the 20 to 30-year veterans.
The problems we face today in bridging the skills gap will be nothing like those we see in the next three to five years. In that time, we will have more and more new employees trained by one-year veterans at best. There is simply not enough time for the trainer to have gained the experience needed to onboard a new employee properly.
Capturing and transferring the knowledge from experienced workers who will not be in place is essential to onboard future employees properly. Companies must be able to extend not just the knowledge (what) but also the understanding (why) to a newer generation. Leaders are two times more likely to focus on building knowledge management capabilities using an approach very different from that of Followers. To replicate this success, manufacturers should adopt these three tactics in frontline workforce initiatives:
-
-
-
Deploy innovative and new training methods.
-
Use intuitive processes and systems to manage training.
-
Implement strong knowledge management governance.
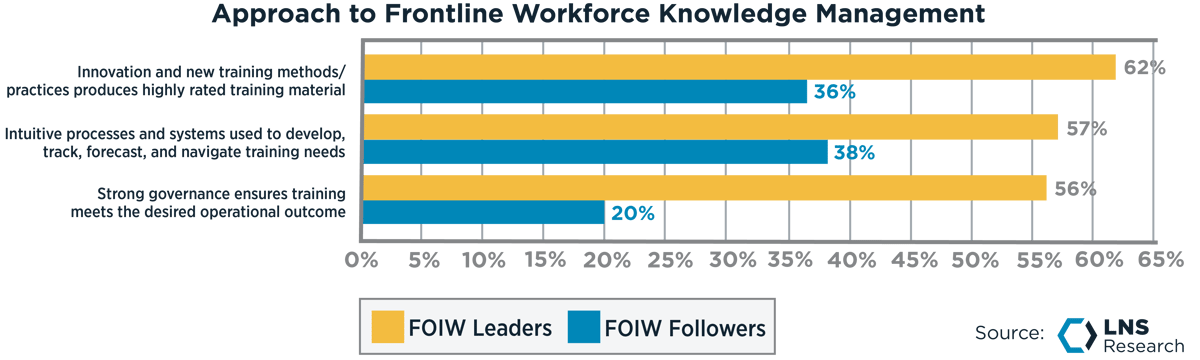
While people will always be critical, the key to safe, reliable, and agile operations is how employers build the foundation to bridge the skills gap. The ability to effectively and efficiently onboard new employees will strongly impact future performance. Manufacturers must invest in and build robust management systems to enable new innovative training techniques and technology.
Digitally Enable New Employees
Many industrials are stuck in the mindset that providing a mobile device to employees is enough. Trends show newer generations who have always known YouTube for answers on nearly everything are much more likely to seek information out on their own. The technology strategy must focus on enabling and empowering the workforce to attract, train, and retain the next generation of employees.
Connected Frontline Workforce (CFW) initiatives are achieving business objectives and meeting enterprise goals by connecting the workforce to the right data at the right time and with the right context. CFW solutions extend conventional mobile applications' functionality and increase the circulation of accurate and timely information to, from, and among the frontline. This more holistic approach enables competent employees, safe work, engaged workers, and agile operations, unlocking a new level of value.
.png?width=550&height=426&name=Connected%20Frontline%20Workforce%20(CFW).png)
CFW applications are a key enabler of engagement for the new generation. The entire workforce also benefits from adopting advanced technology that is capable of alerting workers to hazards, risks, and next steps for tasks being performed. Manufacturing Leaders would do well to consider the ways Leaders are onboarding new employees faster and more effectively with newer, more intuitive solutions:
-
-
-
Connect CFW and Unified Performance Excellence (UPX) applications to track employee onboarding and training effectiveness and continuously improve workforce competency.
-
Leverage Augmented Reality (AR) and Virtual Reality (VR) to support training and skills development, provide personalized content, and enable real-time work support.
-
Build Artificial Intelligence/Machine Learning (AI/ML) algorithm libraries to capture knowledge from experienced personnel and help develop each person into a subject matter expert.
While it is important for manufacturers to provide an environment where technology enables employees, technology alone is not a solution.
Providing Next-level Support
Companies are challenged to find new ways to work more efficiently and effectively with fewer on-site people. What's worse, manufacturers often find that a handful of experienced employees are the difference between keeping things between the lines and running off the track. Instead of seeing this as a disadvantage, many Leaders are starting to create a competitive advantage with this knowledge.
Putting experts in a position to monitor and enhance manufacturing performance in real-time to support the entire enterprise is becoming more of an obvious solution. These cross-functional problem-solving teams can support many more employees simultaneously and provide next-level support across operations. We expect to see increased adoption of Virtual Operations Centers over the years as subject matter experts continue to dwindle and the footprint of operations grows for those who achieve a competitive advantage.
The ultimate goal is to make safer, faster, and better decisions at every level. Manufacturers developing strategies to augment workforce capabilities should look at technology as a way for employees to access the right data, information, and expertise when and where needed. CFW software solutions underpin workforce collaboration and enable the exceptional value of Virtual Operations Centers.
Focusing on the Future
Manufacturers must be able to get future 30-day employees to 30-year performance levels quicker to survive. New employee tenure and time-in position trends require radical changes. Manufacturing can no longer equate job shadowing with volumes of (sometimes outdated or incomplete) policies, procedures, and processes on hand as an onboarding program.
It's never too late to develop a strategy to improve workforce agility and flexibility for future generations. Keep these final thoughts in mind to protect business continuity:
Knowledge management is an integral part of the foundation. You can't give new employees something you don't have. Starting small is better than not starting at all. Sustaining and improving future operations can be achieved through strong knowledge management practices.
Focus on constantly evolving the onboarding program. These steps are not a one-and-done kind of activity. Leaders are creating a competitive advantage by transitioning from Operational Excellence to a Unified Performance Excellence approach. Manufacturers must regularly evaluate the effectiveness of the onboarding process and adjust the program based on feedback and evolving workforce needs.
Prove that you are invested in both individual and organizational success. Employers must acknowledge milestones and celebrate achievements throughout the employee lifecycle. The newer generation is looking for the Total Employee Experience. Enable employees to engage at all levels with the tools needed to build individual competency, regularly share knowledge with the organization, and create paths to advance with Virtual Operations Center roles.
Remain grounded and be realistic. Expecting a new employee to accomplish some of the most complex tasks solo isn't realistic. A clear outline of performance expectations and goals to achieve competencies should exist. Understanding individual learning styles can be key in maximizing the time and resources needed to onboard new employees.
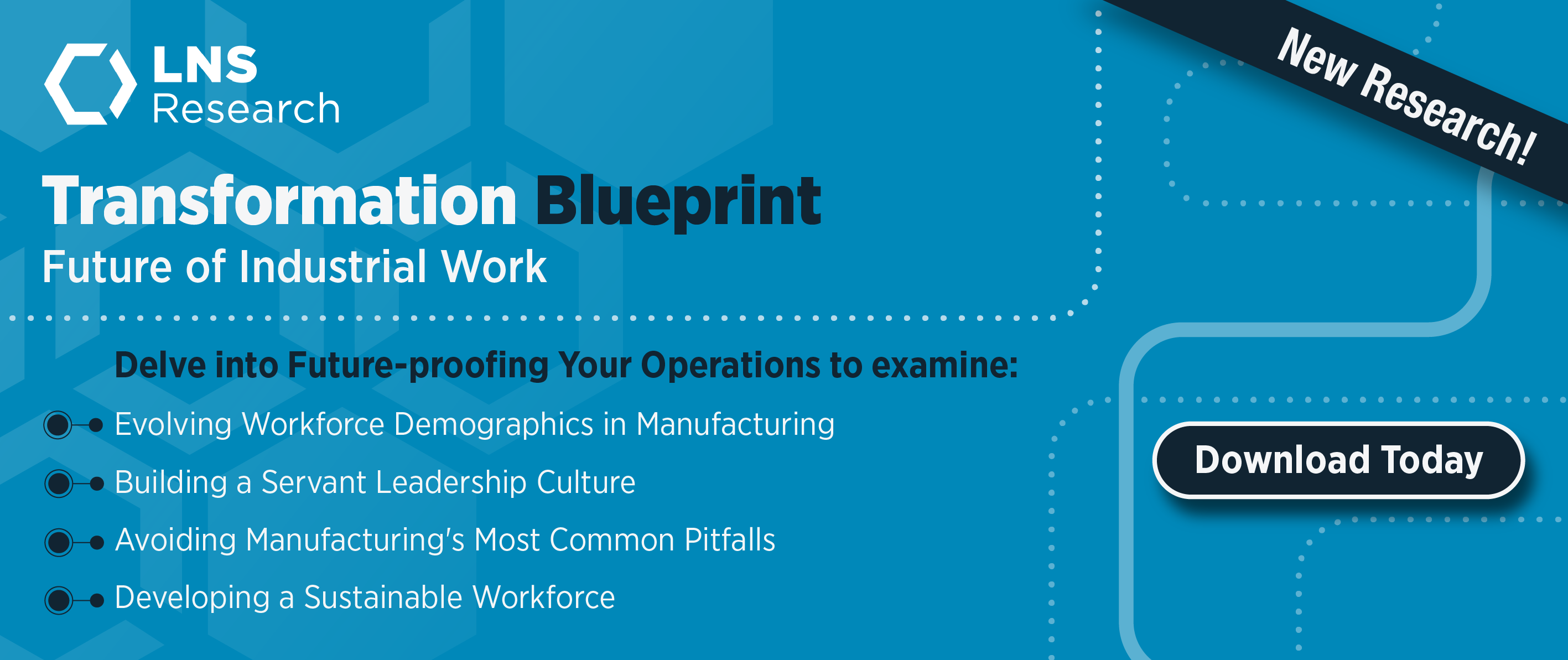