The topic of OEE (Overall Equipment Effectiveness) has been hotly debated. While our research shows that OEE is a commonly used metric, with many world-class manufacturing companies seeing substantial benefits, there are advocates for killing it as a Key Performance Indicator (KPI), claiming it is a distracting measurement.
Overall Equipment Effectiveness (OEE) is the third most used manufacturing metric among Industrial Transformation (IX) Leaders
I will not debate the validity of OEE in this blog post; however, I will ask if we should look at KPIs such as OEE differently in a post-Covid world.
A post-Covid world from a manufacturing perspective
First, let us define what this means. We believe that four manufacturing challenges have become stronger during and after the pandemic:
-
-
-
It has become harder to attract and retain manufacturing workers. Worker absence is still high due to repeated infection of workers or their kids. Many prefer to work from home, and manufacturing does not enable that. LNS Research’s studies show that access to skilled workers is one of the top concerns for manufacturing companies.
-
While Covid-related supply chain issues have been reduced, they are still looming in the shadows. Raw materials have become more expensive, and global supply chains are affected by geopolitical uncertainty. We see companies re-shoring manufacturing and some companies investing in vertical integration by entering their suppliers’ markets.
-
The world has become more uncertain. It has become harder to predict both the demand and supply sides of the economy as we enter unchartered territories. New technologies are challenging established products. Buying patterns have changed. During the pandemic, we saw strong demand for physical goods, but the market is shifting towards services.
-
Capital is becoming more expensive. Rising interest rates are causing increased scrutiny of investments.
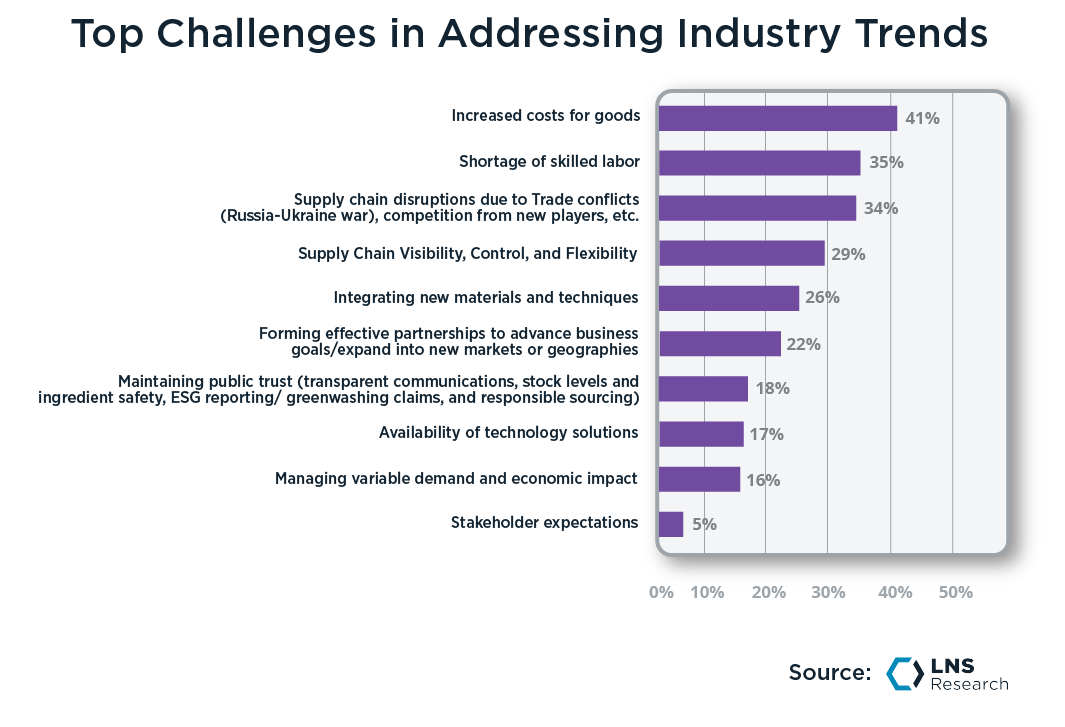
*Up to Three Choices Were Allowed
How does this relate to OEE?
You may be asking how does this relate? Let’s first look at what OEE is.
OEE practitioners will say that OEE is a collection of metrics, not just a single composite metric. OEE is calculated by multiplying Availability, Performance, and Quality, and practitioners will emphasize that all four metrics (OEE and its three components) are essential. LNS Research has written extensively about OEE in previous blogs, such as: Understanding the OEE Formula and Applying the OEE Formula.
While it seems simple to measure and multiply three numbers to calculate OEE, the reality is more complex:
-
-
-
There are considerable debates about how to determine the time equipment is Available. A maintenance engineer may argue that the equipment is available for production anytime it is not stopped for downtime or maintenance. In contrast, a scheduler may say that the equipment is only available for production at the time it is scheduled to produce.
-
Similarly, challenges are associated with the Performance calculations. Some manufacturers will argue that the performance can be above 100% if the line is optimized to run faster than its rated speed, whereas others will adjust the rated speed and, in effect, penalize the engineering work done to make the equipment faster.
-
Finally, it is often challenging to measure Quality in line. Sometimes the products are sent to a lab where the results can become available days after production. In other situations, the quality issues are not detected until years after being sold when the product fails in the market.
A common trap is to choose the wrong scope and time granularity for the OEE measurement. It is meaningless to aggregate a single OEE number for a plant or a business unit as it does not identify where the issues originate or how to address them while failing to empower the people who could correct the problem. Similarly, it is likely counter-productive to measure OEE on non-producing assets, such as motors, and to measure OEE in real-time on a second-to-second basis.
Suppose you correctly measure Availability, Performance, and Quality, and look at OEE as a single composite calculation and therefore don’t treat OEE as a collection of metrics. In that case, OEE becomes a measure of the number of good-quality units produced in a time period compared to the theoretical maximum number of units that could be produced for the same time period. The issue is that the single metric makes some significant assumptions about what manufacturing companies want to achieve and what their constraints are. These assumptions may have been valid before Covid, but the post-Covid challenges listed above have amplified the single metric concerns.
How should manufacturers choose their KPIs?
Well, the answer to that is simple. First, don’t choose a KPI just because everyone else is using that KPI. LNS Research has developed an Industrial Transformation (IX) Framework to guide your journey. The right place to start is with your business objectives. Take these business goals and formulate them in manufacturing terms. Are you trying to grow your existing business? Enter new product segments? Maximize profitability? Increase customer satisfaction? Increase product quality? Reduce emissions? Serve the market better? Reduce working capital? Each of those objectives will demand a different set of KPIs.
%20Framework-1.png?width=901&height=601&name=Industrial%20Transformation%20(IX)%20Framework-1.png)
Start with your business objectives
I am a big fan of Lord Kelvin’s quote, “You cannot improve what you cannot measure.” You must analyze the manufacturing business objectives and then identify how you will measure if you are achieving those objectives. With this in mind, you will quickly see that OEE is a good measure if you want to produce a given product's highest number of units. Still, it is a poor measure if you want to optimize the utilization of scarce raw materials or adapt production to the personnel skillset available in the plant. This is where the post-Covid world becomes relevant. The objectives and priorities have changed based on the new constraints.
We can see these challenges in many industries. A great example is automotive suppliers, as they are professional manufacturing companies with robust Continuous Improvement (CI) programs and world-class OEE performance. If we look at the automotive industry through the effectiveness lens, then there is little room for improvement that would justify investments. However, the industry has gone through a massive transition to fuel-efficient and electric vehicles and new technologies such as autonomous driving and over-the-air software updates. These changes in consumer preferences have dramatically changed the product mix and led to an increased focus on New Product Introductions (NPI). However, it would be a substantial competitive win if they could keep their OEE at the current level while doubling their NPIs. Automotive suppliers need a step change in behavior and therefore need to recalibrate their metrics.
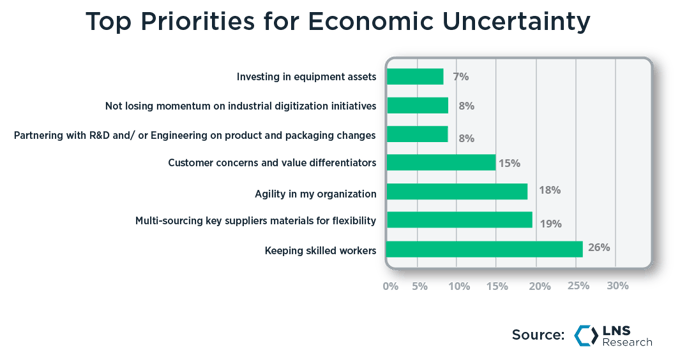
We see similar shifts in materials and energy companies. They have been running flat out in 2021 and 2022. They could sell anything they could make, and the margins were unprecedented. Exxon Mobil made almost $13B in profit in Q4 2022, and Saudi Aramco made $161B in 2022. Things have changed in 2023. The Brent crude oil price dropped from more than $130 per barrel in March 2022 to about $70 in March 2023. Some production assets that were hugely profitable in 2022 are now barely scraping by, and the focus has shifted from effectiveness to profitability. Just continuing to maximize OEE in 2023 and 2024 may not be the right strategy, and some assets may need to be taken offline until the margins improve.
OEE and other KPIs must be part of a corporate initiative, and you must ensure that the user of any KPI is identified so that someone will use the information to drive change. Don’t assume that the KPI is relevant for an executive in your organization if you don’t know how they will use it.
I promised you that I would not debate the validity of OEE. There are good ways to use the metric to optimize behavior intuitively. Some examples are:
-
-
-
Drive continuous improvement of the same asset over time.
-
Share best practices across similar asset types across the organization.
-
Identify opportunities for focused and timely investigation.
Summary
We recommend evaluating your business objectives and identifying what has changed post-Covid. Select KPIs that measure how well you are achieving those business objectives. Covid changed the world: It is possible that the business objectives and associated constraints have moved away from equipment effectiveness and towards other factors such as profitability, raw material availability, flexibility, NPI, and labor shortages. OEE may still be a relevant tool for you. If it is, we recommend that you look at OEE as a collection of KPIs, not a single composite KPI.
Remember that OEE can be a polarizing metric. Although it is one of the most used metrics, you will find one detractor for every two proponents. Organizational alignment, clear expectations, and effective change management are required to ensure that the metric creates more value than noise.
We encourage our members to leverage the LNS Research library, which contains numerous articles and blog posts on OEE and related topics.
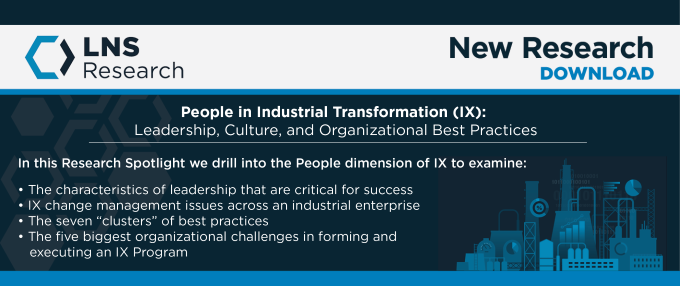