LNS has long focused on Operational Excellence (OE) as part of our Digital Transformation (DX) Framework, now Industrial Transformation (IX). In 2013 and 2014, we talked about Operational Excellence as a journey and stated that people, processes, and technology are the underpinnings of Operational Excellence initiatives.
In 2016, we noted that most companies have Operational Excellence initiatives in some form or fashion for 10 years or more. Often, these initiatives also incorporate the multiple management systems and continuous improvement capabilities of the firm like Lean or Six Sigma.
Later in 2016, we represented OE through the lens of a set of core pillars that acted as the foundation of the OE platform. Given the impact of disruptive digital technologies, we expanded on these pillars, where we, for example, coined APM 4.0 as a collection of components. We based much of our research efforts on investigating the market trends and technology directions in each of these pillars, even though we advocated for a more integrated holistic view.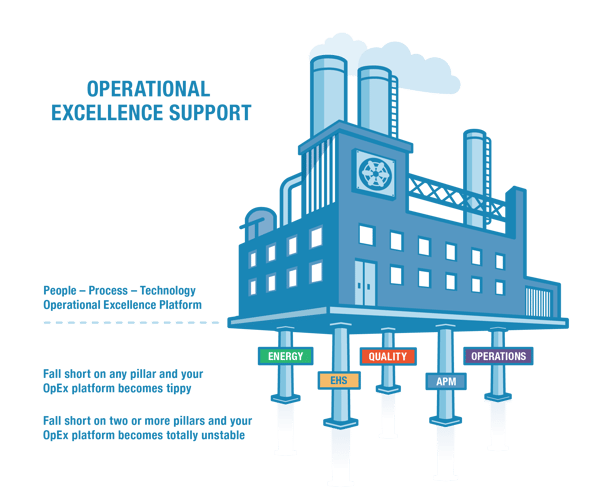
Figure 1- Operational Excellence Support
Now in 2020, as we deal with the COVID-19 crisis, leading companies have increased their interest in remote and even autonomous operations. We asked ourselves how companies can manage through the crisis to land in a better place – in whatever the new normal will be – and what is it going to take to get there. But then we stepped back and asked, “Do we need to revisit the definition of OE, and how do we make OE actionable?”
Defining OE
Our research revealed that most companies still have an Industry 3.0 view of OE expressed as a Continuous Improvement program. CI is described as the ongoing effort to improve an organization’s processes, products, or services, taking place incrementally over time rather than through some breakthrough innovation or step-change in performance. OE, on the other hand, is said to be a mindset that embraces certain principles and tools to create sustainable improvement within an organization, the principles and tools primarily referring to Lean, Six Sigma, and Kaizen.
We looked at various definitions from academics to management consulting to the Institute of Operational Excellence to operating companies themselves. Perhaps the best description, but not strictly a definition, comes from DuPont, a pioneer in OE concepts: “OE is the application of principles, systems, and tools to engage and focus everyone’s efforts on meeting customer needs and continuously improving process performance. It focuses on minimizing and managing downside risks while maximizing an operation’s performance and shareholder value.” DuPont’s work in OE brought out two concepts that most other definitions overlook: first, the critical role of leadership, and second, the focus on “Operational Discipline (OD).” By OD, we mean the, “deeply rooted dedication and commitment by every member of the organization to carry out each task the right way every time.” And so DuPont rightly highlighted the emphasis on workforce capabilities and culture as keys to OE.
The Opportunity
And so we have arrived at a revised definition that says OE is a journey, not a program, in essence, a way of doing business, and not just CI process and tools. But then when we looked at how companies were executing OE and found that the methods and tools were stuck in the various silos of non-integrated software, that is in multiple systems EHS, APM, EAM, Quality, HR, etc. OE 3.0 has mostly been reactive, about safety and compliance, and not about comprehensive, proactive risk management. And until recently, EHS software has carried the risk, safety, and PSM ball, but it’s been more about tracking and recording than proactive execution. If OE is about a holistic approach, then where is the holistic system to support its execution?
The vendors claiming the OE and risk management space are battling each other for position, expanding into each other’s territory. This makes it difficult for operating companies to choose OE solutions and reduces their willingness to change to something better because they do not know or understand the path to a better outcome and its expected ROI. Thus, the tendency is to do nothing or wait until the market evolves. Also, software initiatives are often driven by departmental needs, so different vendor alignments often propagate as a result, even when common functions are shared (e.g., mechanical integrity with the PSM and inspection organizations). LNS believes the operating companies are missing an opportunity for proactive change for the better, especially given the need for resilient operations in the face of the current circumstances. Clearly, there is an opportunity for innovation, especially in light of the new capabilities enabled by digital technologies.
OE Framework
So what’s needed is an Integrated OE Execution System that effectively and seamlessly integrates the key OE activities:
- Strategy
- Integrated Processes that transcend departmental boundaries, including:
a. Asset and Process Integrity
b. Quality
c. EHS
d. Process Safety Management
e. Operations
f. Workforce Competency, Effectiveness, and Efficiency
- Management of Change
- Performance Management
- Operational Risk Management
This is the OE 4.0 hill to climb.
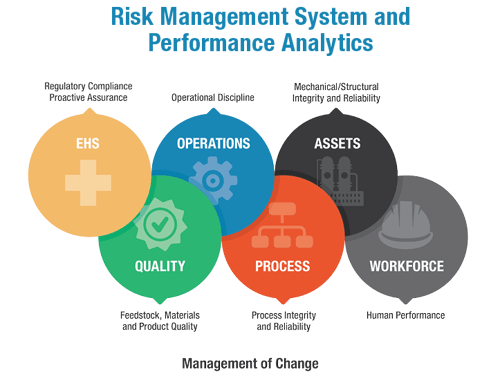
Figure 2- Operational Excellence Framework
Path Forward
So, where does this leave us? First, it leaves us with a definition of OE 4.0 that centers on sustainable value creation through a holistic approach supported by an enabling execution platform. And what of the OE execution platform? Good question. Does such an enabling platform exist? We shall see.
The answer to those questions and many more are the subjects of our future research. We will focus on the differences between process improvement, process execution, and process transformation, with the objective of how to figure out how to bring these approaches together and align for the future.
Finally, how does this all fit in toward delivering remote operations and the autonomous plant? What has to happen to cross the bridge too far and make autonomy a reality? Stay tuned.
To learn more, see our spotlight on Toward Operational Excellence 4.0.
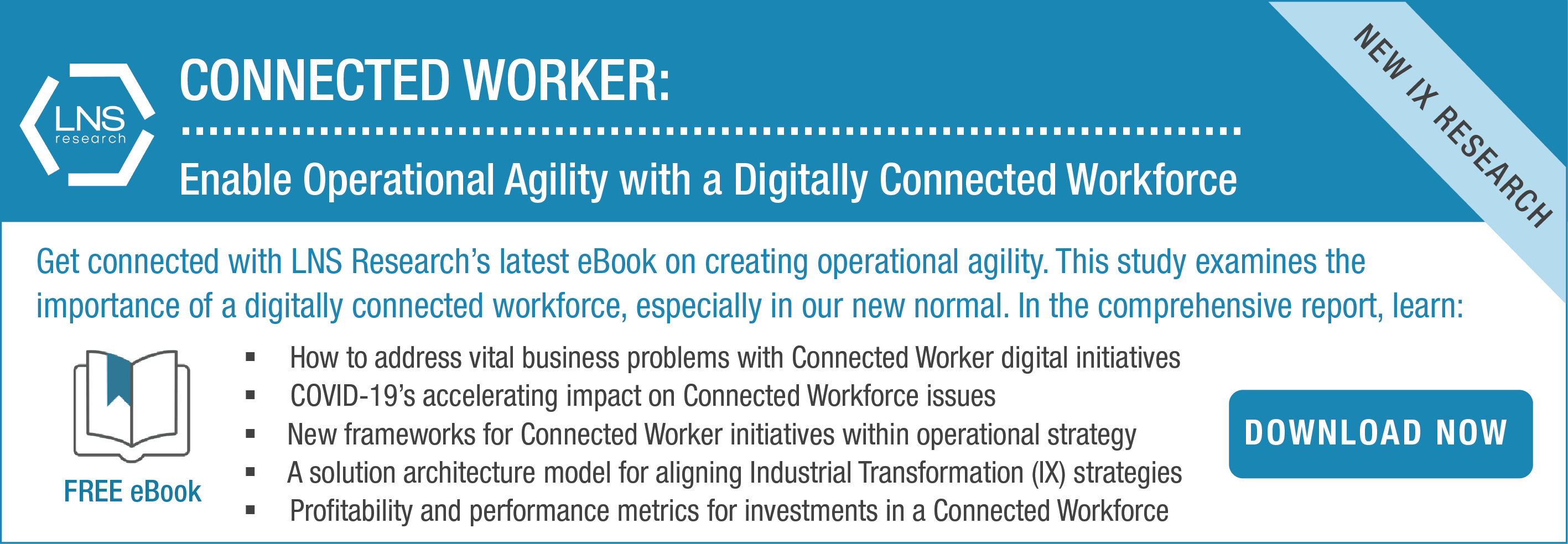