Since the advent of Manufacturing Execution Systems (MES, or MOM for those who prefer) in the late 1980s, life sciences, and especially pharmaceuticals finishing and packing, led the way in useful MES solutions. Some would argue that MES for pharma has reached maturity and there are few gains to be made. At LNS Research, we believe that change is just beginning and it is time for the pharma software industry to wake up or get severely disrupted by new players.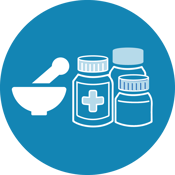
Many pharmaceutical companies, ranging from boutique startups to the global giants, have active Industrial Transformation (IX) programs that foresee structural changes in the way they operate. Existing pharma MES systems provide the necessary functionality for most operations but are hard to maintain, inflexible, and do not provide a data platform for other parts of the enterprise. Such integration will, inevitably, be a part of IX programs.
Looking Back
Early MES systems mostly grew out of industrialized computing platforms on top of which manufacturing applications were programmed, usually for specific projects. The opportunity to use these early MES solutions for pharma projects was clear: batch records were a constant headache for pharma manufacturers and converting from paper to glass could help enormously. Pharma MES startups proliferated in the 90s. Automation companies saw the opportunity to combine MES with control systems in the pharma industry; integrated solutions could generate a large volume of high-margin projects. The first big change in pharma MES saw the majority of the independents bought by control companies. This change should have seen large investments in pharma software but, in reality, the MES teams stayed together and continued to operate much as before. Indeed, some pharma MES teams were subsequently sold off and the overall market changed little.
.png?width=630&name=Plant%20Gas%20Pedal%20Performance%20Optimization%20Diagram%20final%20(002).png)
Steady Change
The US Food and Drug Administration (FDA) thoroughly encouraged pharma companies to go digital and defined what electronic batch records (EBR) should look like in the official regulations, 21CFR Part 11. EBR certainly sped up batch record submission and checking, but it was not clear that the manufacturers were making money from this. As other regulations arrived, the FDA continued to encourage the move to digital. For example, in serialization and genealogy, the rate of deployment hardly increased and we see today many plants continuing with paper records and, hence, failing to improve product safety and manufacturing efficiency.
Another issue with current MES is that the automation companies that bought (or developed) pharma MES have since put a lot of effort into more general software platforms for Industrial Transformation (IX), and have not redesigned their MES to benefit from the new architectures of both applications and data. The general MES market is moving fast due to IX and we are starting to see disruptors that are moving toward an MES that is integrated into an IoT platform and is made up of semi-independent apps that allow extensions to functionality as desired.
A few years ago LNS Research defined different MES Architectures as the "Seven Lives of MOM," starting with no MOM and ending with an IIoT platform and a collection of apps. This is exactly where the leaders are going today.
Moving to IX
There is an understanding in the pharmaceutical industry that Industry 4.0 and other Industrial Transformation (IX) programs need to be extended to support all the regulations and good manufacturing practices (GMP) used by the industry. The International Society for Pharmaceutical Engineering (ISPE) is doing a lot of useful work in defining what is important for what they call Pharma 4.0, and ensuring that manufacturers have access to an extended view of IX for pharma. It is clear that MES functionality will be an important part of their Pharma 4.0. However, the old way of having everything connected to MES for operations will not deliver the value of data beyond the shop floor. It is easy to continue with the existing MES solutions and build IX around them but the real benefits will start to accrue when an IX architecture supports manufacturing data, including everything that is required and generated by manufacturing operations.
Advice to pharma manufacturers is clear:
- Get rid of paper – you should have done it ages ago. Concentrate on plants with little
automation rather than high-tech modern plants: if you know what is happening in manual plants by recording everything in your EBR, mistakes will be fewer and batch releases will be earlier.
- Going beyond traditional MES requires pharmaceutical companies to invest in new technology. The offerings are still nascent, and so the most efficient way forward is to partner with a startup pharma software company, build a modern IIoT-based pharma operations suite of apps, and try it in your plants.
After the previous step, make your MES solution an integrated part of your Industrial Transformation (IX) journey.
You must include the core requirements of IX:
- Data models, a complete data architecture – bringing it all together through an operational data lake. It is nearly impossible to execute an IX strategy without solid data across the enterprise, and building a modern MES will be viable with solid data underpinning the whole.
- Many large pharma companies have venture capital investment funds and this is an opportunity. In the oil and gas industry, Aker BP invested in a successful industrial data ops platform, Cognite, and has driven rapid growth and deployment of the platform for Industrial Transformation (IX), as well as innovation throughout Aker BP.
Where are the Vendors?
What should vendors do? It is very difficult to give a generic answer but we can look at a couple of typical cases. The vendor market for Pharma MES is full of players that have been around mostly for decades. As we explained, many are now part of large automation and industrial software companies. We will choose one independent and one automation vendor and look at a potential disruptor.
Werum, now belonging to Körber but acts as an independent, is the biggest player in the secondary MES pharma market. It has successfully maintained its long-term relationships with Big Pharma and is on the shortlist for most new programs. However, its differentiation in the marketplace comes from services and delivery rather than selling market-leading technology. Werum is a leader in pharma MES but needs to change to support a wider IX strategy, perhaps with partners to achieve flexibility without losing past reputation and delivery.
We are starting to see changes in the automation vendor community and their area.
A number of partnerships that deserve to be watched:
Honeywell has invested in AIZON to drive data integration in Pharma operations. Emerson has made similar commitments to Fluxa that provide process knowledge management to aid collaboration across different phases of the drug life cycle. Both of these are in the early stages of collaboration and deserve to be watched. Whether they will lead to the next-gen MES for pharma remains to be seen.
Tulip is a modern IIoT platform with an ever-increasing set of apps offered by the vendor to meet MES needs. As they develop FDA-compliant apps, they have an opportunity to disrupt the monolithic pharma MES market by offering a platform for new apps, the benefits of low code/ no-code app building, and a robust data platform from which to deliver value through manufacturing data.
The future world of industrial software in pharma will be in stages:
- More of the same with partially integrated MES for pharma will be the status quo for a while, and
- A modern industrial transformed enterprise with apps to cover MES and many other functions will follow. The key question is when and who will be the leaders; ambitious pharma manufacturers and vendors need to be among those leaders, soon.
The industry needs some serious nudging to become once more a place of leadership in manufacturing operations software. Only moving fast to the second approach will enable that.
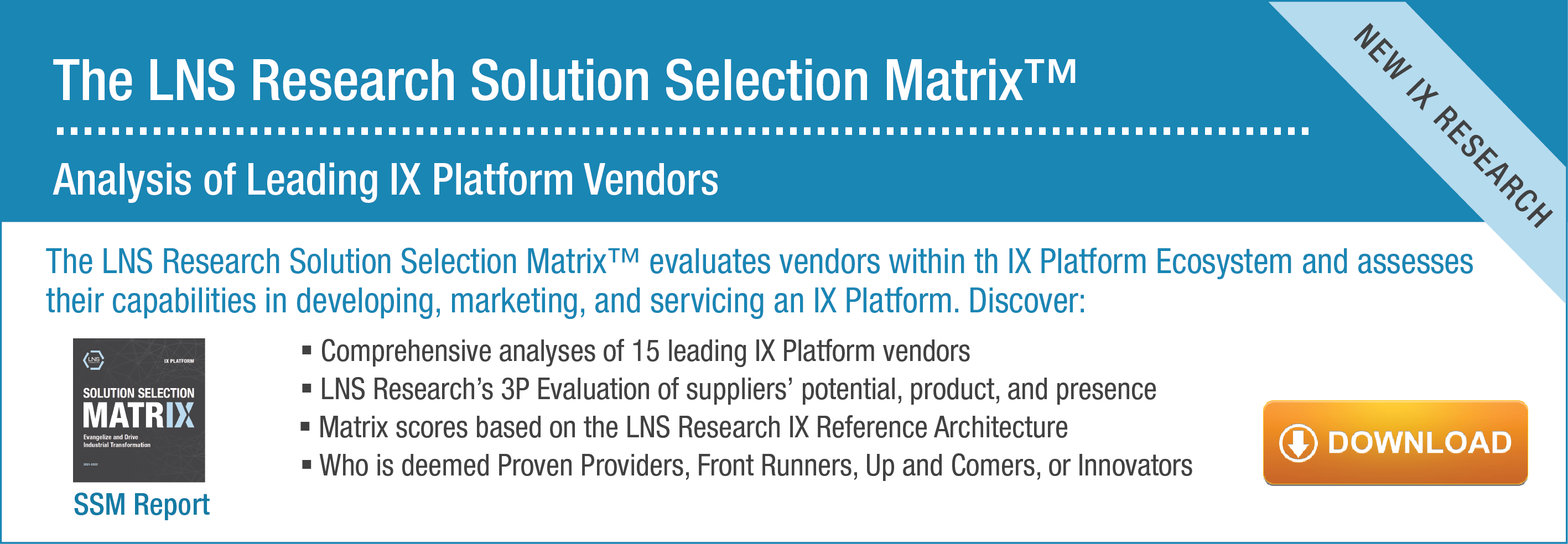