Unified Performance Excellence (UPX) involves embedding the process and management of Performance Excellence in the digital environment. This approach leverages advanced digital tools to bridge the gaps in knowledge, speed of execution, and results commonly associated with traditional operational improvement methods.
Traditional continuous improvement management programs suffer from several headwinds, including:
-
-
-
Retaining trained practitioners
-
Gaining and maintaining momentum
-
Long waits for results
-
Rapidly shifting priorities
-
Lack of data to support the discovery of root causes and solutions
-
Asynchronous to manufacturing operations
These challenges result in most traditional continuous improvement management programs struggling to gain and maintain momentum. In our recent UPX research, 75% of manufacturers reported struggling to sustain momentum, even after initial project successes. Fully 20% of survey respondents report having zombie programs, those that are deployed in only a few plants. Zombie programs create confusion and lead to the perception of a “program of the month” approach.
These struggles are endemic to Performance Excellence in the Industry 3.0 world. The root cause is that these initiatives are rooted in the 3Ps:
-
-
-
People
-
Policies
-
Procedures
Accountability and sustainment are challenging to achieve through a management approach with no supporting infrastructure to help maintain it.
Industry has been on the digitalization journey for over a decade now. Performance Excellence programs lag behind in adopting digital technology as Industrial Transformations (IX) have progressed from pilot to scaled deployments.
In this research, we see three key areas where followers fail to achieve real value for their efforts:
-
-
-
Keeping UPX and IX teams separate creates confusion
-
Building your UPX practice on island platforms
-
Being the “Ostrich with its head buried in the sand” where threats to agility, flexibility, and resiliency are concerned
Keeping UPX and IX teams separate
Heads of Operations today have many things flying at them all at once. One of the big challenges that a COO, VP of Operations, or Global Supply faces is coordinating all of their teams to the greatest effect.
Figure 1: UPX Leaders merge UPX and IX Teams
These teams operate as two separate silos with no common vision, language, strategy, or change management plan for the organization, which can result in:
-
-
-
Confused and overwhelmed plants with similar but different initiatives, workshops, and tools
-
A disconnect between process and technology, i.e., the problem-solving techniques deployed in manufacturing aren’t aligned with the deployment of advanced industrial analytics
-
Different assessments and prioritization of challenges, use cases, and tools
-
Strain on the same resource pool to support separate initiatives that are not synchronized, coordinated, or aligned
Followers are three times less likely to align and merge their Digital and Performance Excellence Teams (Figure 1). This creates confusion for plant teams, wondering which priority to focus on with the limited resources at their disposal.
Building your UPX practice on “Island” platforms
Traditional Performance Excellence is done on paper or flat file applications like Word, PowerPoint, and Excel. Sometimes a Statistical Analysis package is used on manually assembled data to determine causes and potential actions asynchronously to the studied process. Very primitive.
Our UPX research suggests a step in the right direction is adopting a “build with what we have” approach by building UPX on an existing Industrial Transformation software package such as an Enterprise Quality Management Software (EQMS) system.
This approach is a good proving ground for developing and refining your preferred method. Still, it will quickly run up against the limits of capabilities from today’s EQMS solutions when trying to scale across the organization.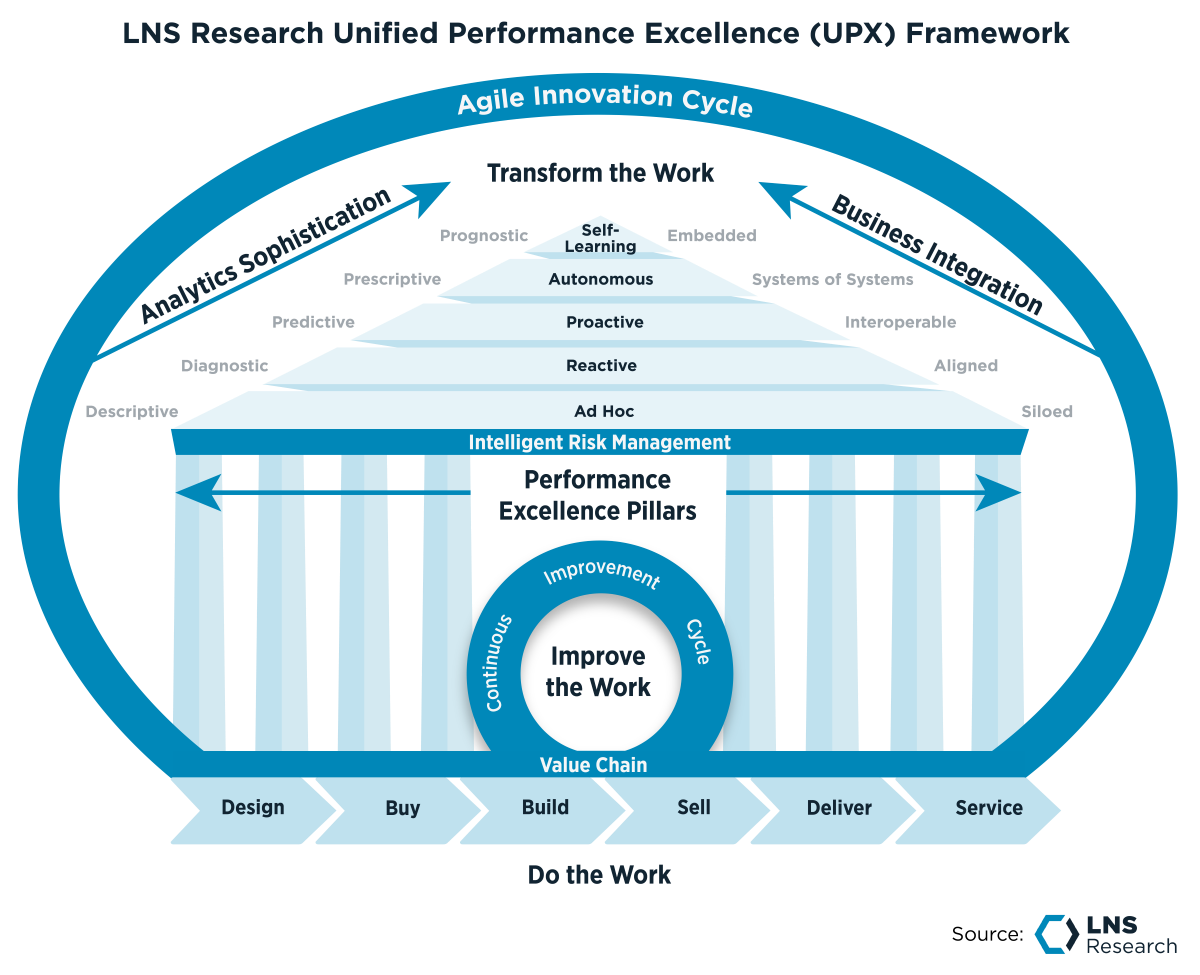
Figure 2: Digitize Performance Excellence to gain speed and consistency
Today’s EQMS solutions are mainly “form-based” offerings with some citizen-developer-enabled features. EQMS vendors are experimenting with Generative AI mainly for information-gathering use cases, where scraping the platform for similar information to a particular event is the request. This is far from the use cases for advanced digital tools in support of UPX, where AI and Digital Twins are heavily used to add insights and speed time to results.
A Low Code/No-Code platform with embedded data source connectivity, Digital Twin, AI and ML, and Advanced Industrial Analytics is part of the solution and is the proper home for UPX to scale across the organization (Figure 2).
Ignore threats to the sustainment of your operation at your own peril
Manufacturers have endured several “Hundred Year Storms” over the last 3-5 years, starting even before the COVID pandemic; there was a significant labor crunch brought on by a booming economy and statistically full employment, then things shifted rapidly with the pandemic, post-pandemic labor migrations, and rolling supply chain shortages of materials, among other changes. Heads of manufacturing operations have got to be tired right now from looking over their shoulders all the time for the next threat!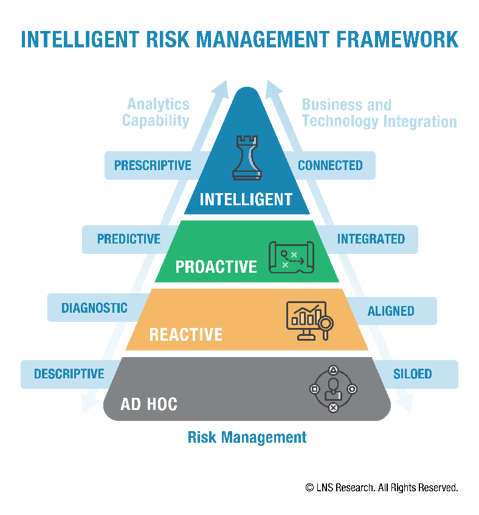
Figure 3: Build the Risk Dashboard for Agility, Flexibility, and Resilience
Assuming that everything is now all right and will stay that way is a recipe for upset to operational agility and flexibility. The global supply chain is still in an upset period and will likely remain that way for a few more years. Manufacturing organizations should be hardened to unexpected supply chain issues.
UPX Leaders are building a digital, near-real-time view of operational risks. This “control tower” approach enables proactive monitoring and management of potential impacts on operational agility, flexibility, and resiliency (Figure 3). In this age of geopolitical turmoil, economic uncertainty, and growing pains coming out of the global pandemic, it is essential for operations leaders to keep their eye on anything that could potentially shut down operations.
Recommendations for Chief Manufacturing, Operations, and Supply Chain Officers
-
-
-
Appoint a senior executive to focus on the Transformation strategy. With so many challenges flying around, carve out someone from the day-to-day to focus on strategy, change management, coordinating, and bringing together the many teams with a piece of responsibility for transformation. This role should have a broad scope, spanning functions and the plant network. Your Plant Leaders will thank you for bringing order to the chaos.
-
Move from “island” platforms to enterprise solutions. Refine and perfect the approach on an island platform, then move to an LC/NC Interoperable platform to leverage data connectivity and advanced digital tools to scale. UPX residing on a highly interoperable platform with citizen developer functionality embedded transforms UPX from an asynchronous improvement activity to the improvement engine for Industrial Transformation.
-
Start the hard work of defining risk frameworks and making risk-based decisions about threats to agility, flexibility, and resiliency. Each company is different regarding unique threats to the sustainment of manufacturing operations. Each company has its own unique tolerance for various threats. These factor into the development of a company-specific risk framework and thresholds. Risk frameworks are foundational to achieving near-real-time Intelligent Risk Management, then connect data to these frameworks to enable the real-time risk dashboard.
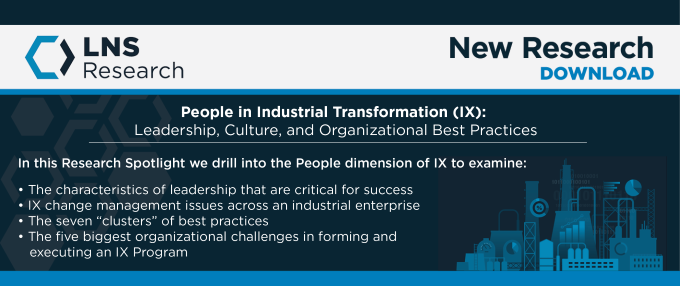