The majority of today’s business professionals will be familiar with the famous quote by management consultant Pete Drucker, “Culture Eats Strategy for Breakfast," which implies that no matter how solid a business strategy is, its likelihood of success depends on the people executing it and the organizational culture that surrounds them.
While being applicable to any business, LNS Research believes that organizational culture plays a critical role in today’s manufacturing companies and has listed it as one of the nine fundamental elements of an Industrial Transformation (IX) program.
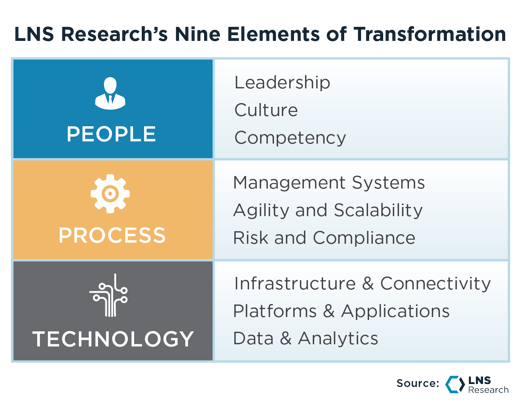
In addition to being one of the most crucial pieces of an Industrial Transformation program, Culture is also unique. Unlike the other elements, Culture cannot be easily quantified through traditional methods.
Even in cases where it can be measured (through some of the newer employee engagement tools), it is often difficult to improve it, as Culture primarily resides in people’s attitudes and behaviors. More often than not, the only solution to culture problems is to change the people or change the people.
As such, I believe that an organization’s culture is the heart and soul of any transformation program. In this blog, we will break down organizational culture into its fundamental blocks and answer some of the key questions faced by today’s manufacturing companies on this topic.
First of all, what is culture?
While the term culture in today’s corporate work environment is often just limited to perks such as bean bags and ping pong tables at the workplace, happy hour, and team building retreats, it is, in fact, much more than that. Several academic and industry frameworks, such as the Schein Culture triangle and the Shingo model, clearly define organizational culture.
Regardless of which definition or framework you go with, an organization’s culture is mostly the collection of traits, behaviors, unspoken rules, open secrets, and the set of shared values followed by the employees and the organization as a whole.
Benefits of a strong, positive culture:
As mentioned above, culture differs from other elements of transformation and does not have the same value proposition as other elements, such as technology or management systems. Unlike most other elements, cultural practices don’t yield tangible financial results immediately.
On the contrary, a positive organizational culture provides numerous intangible benefits, such as increased transparency and smooth communication among different teams. It enables, motivates, and incentivizes employees to go above and beyond the bare minimum required in their day-to-day job. It also leads to less friction and office politics between multiple teams, enabling them to identify, prioritize, and resolve cross-functional problems much earlier.
For example, the data (shown below) from a recent LNS Research survey proves that companies, where plant-floor workers welcome data-driven decision-making are substantially more likely to successfully transform their operations than companies where they are wary of it replacing them.
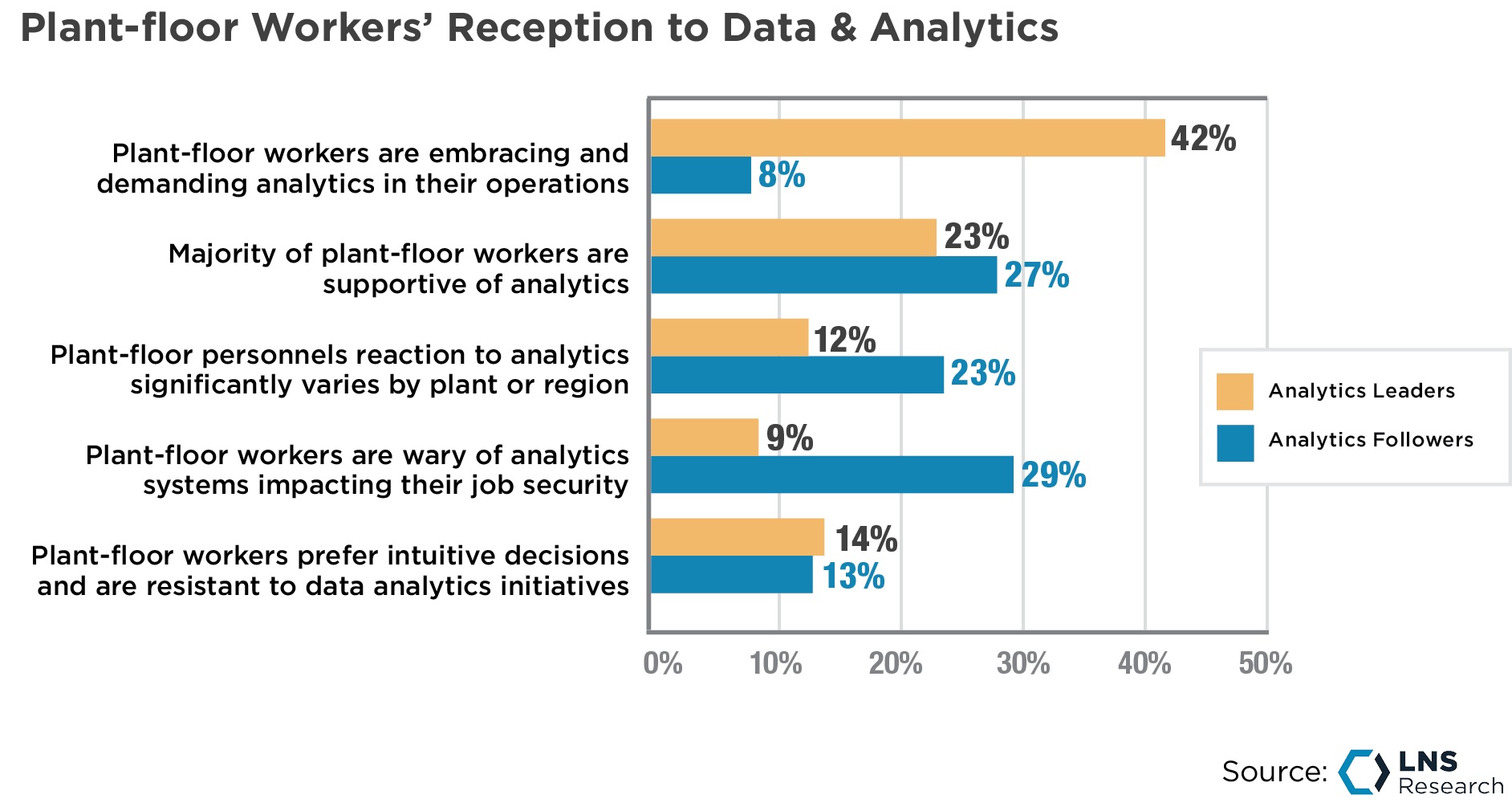
In this case, there are several underlying causes of the frontline’s apprehension towards digitalization that a positive culture can change. Through transparent communication, coaching, and collaboration, leaders can help demystify the value of digitalization for the frontline to see how it can enhance their performance and not replace them.
Additionally, bringing them along the transformation journey by envisioning new job roles and career paths for them will improve productivity, turnover, job satisfaction, and wellness of not just the current but future generations of the frontline workforce.
The many faces of organizational culture:
For today’s industrial organization, culture exists in many shapes and forms. In this section, we go over some common types of culture today’s companies need to focus on as part of their Industrial Transformation programs.
-
-
-
Culture of Operational Excellence: Operational Excellence is one of the common continuous improvement frameworks followed by manufacturing companies that focus on maximizing value to the customer. Instilled in the center of these Operational Excellence programs is a culture of operational discipline that urges all employees to do the right thing, the right way, at all times.
-
Lean culture: Born out of the Toyota Production System, the Lean culture embodies a strong commitment to eliminate several types of waste on the factory floor, reduce inventory through just-in-time production, and thereby maximize value to the customer.
-
Data-centric culture: A data-centric culture involves companies moving from relying on intuition-based methods to quantitative and data-driven decision-making.
-
Culture of Quality: In the majority of industrial companies, the Quality function is seen as a policing authority that has to keep operations in line as opposed to working with them. This organizational disconnect has led to subsequent challenges. It has prompted Quality leaders to build and nurture a Culture of Quality to ensure that quality is seen as the responsibility of every function, not just Quality teams.
-
Culture of Safety: A culture of safety is a set of principles, operating procedures, and guidelines followed by companies to prevent workplace injuries on the factory floor, increase the productivity of the frontline worker, and minimize the risk of failure.
Summary & Recommendations:
Organizational culture is a critical and unique element of Industrial Transformation programs; it defines how well the broader organization embodies and executes the strategic vision. A good culture nurtures symbiotic relationships and trust between different groups, silos, and reporting structures – all the way down to and especially including frontline workers.
To be able to succeed in Industrial Transformation, LNS Research recommends industrial and manufacturing companies proactively focus on and invest in their organizational culture by:
-
-
-
Understand your current culture before changing it: Take a hard look and critically assess what your culture is. Then begin at the mission and vision level and have senior executives exemplify the culture shift religiously before cascading down the organization.
-
Taking a holistic approach: A culture of quality is not just for the Quality teams, and a data-centric culture is not only for IT.
-
-
-
Bringing the employees along on the journey: At the end of the day, it’s the people who make or break a transformation program. Empower, motivate, and incentivize employees to shed the “not-my-problem” mindset and replace it with a “problem-solving” attitude to transform the business and their careers along the way.