There is some good news out there regarding Quality 4.0. programs. First, the prevalence of Quality 4.0 programs is growing. The number of Quality 4.0 programs nearly doubled from 2019 to 2021. Second, Quality 4.0 Leaders are reporting double-digit improvements in several key business metrics, including Cost of Goods Sold (COGS) and Revenue. However, all is not sunshine and roses in Quality 4.0 programs. More than half of the deployed programs are underperforming on their targets. Eighty percent of Quality 4.0 initiatives are not led by the Quality Leader in the organization. A recent series of LNS Research Spotlights and blog posts reveal several reasons for the risk of failure on Quality 4.0 transformation initiatives, including:
-
-
Too much focus on technology
-
Quality Leaders not leading
-
Not focusing on business outcomes
-
Compliance Mindset
There is one common thread running through all four issues reported above, the lack of a strong Culture of Quality within the organization.
A culture of Quality might mean that everybody is doing things the way the Quality function wants them done. This mindset is akin to the Quality function trying to push a rope. A Quality organization within a larger manufacturing company will never be the controlling entity for the actions of the company. This is a losing mindset. Another definition of Culture of Quality would be something like “doing all things with excellence”. This is a concept that everyone can get behind and visualize. I think Quality personnel believe they are doing the second, but the approach is more like the first definition. One of the side effects of Quality being too focused on compliance is that they tend to be rigid and structured in their approaches. Quality teams have a difficult time thinking about issues in the business context and discussing them in the language of business.
Most manufacturing companies do not have a separate Head of Quality reporting to the top leadership (call it CQO, SVP of Quality, or whatever you prefer). Most organizations have Quality reporting into Operations, R&D, Engineering, Supply Chain, etc., depending on the company's preference and perception of the quality role. Quality is one of several support roles that help the primary value driver achieve the business goals.
Even if there is an executive-level leader of the Quality function, that person has a lot on their plate and many temptations to get dragged down into the weeds.
Most Quality leaders over-emphasize their role in compliance, to the detriment of other critical roles they must play. Seventy-one percent of quality leaders report their priority as compliance-related activities. This over-emphasis on compliance leads to a perception by business partners that quality is the policeman and not a strategic partner. This reality leads to a lack of engagement in transformation initiatives. Only 20% of Quality 4.0 leaders report that the quality function is leading the transformation. Quality 4.0 transformation is being done To quality, not With or By them.
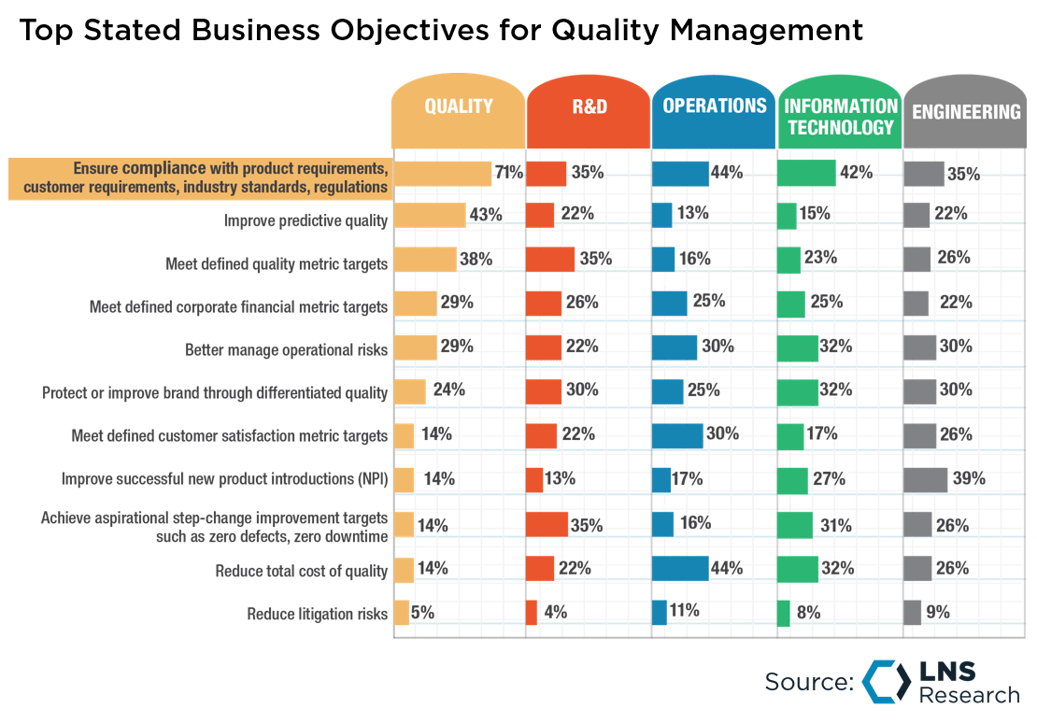
What are the solutions?
First, Quality 4.0 is not about technology. Seventy-two percent of Industrial Transformations fail in part because of an over-focus on technology. I call this phenomenon the “solution in search of a problem” approach. Since transformation is not about technology, what is it about? Here at LNS Research, we define a transformation as “the proactive and coordinated approach in leveraging digital technologies to create step-change improvement across the value chain.” In other words, leveraging digital tools and technology to fundamentally change the way you do business. Changing the way we do the business of Quality is the same as any major change program in a company. It must have a few key aspects checked off to help it have a chance of succeeding.
Vision:
The business of quality is a tough one. In many companies, Quality is seen as the “Department of No”, that rejoices in finding defects. Quality often deals with customer complaints, defective products, the pressure to ship marginal products or come up with the justification for not shipping them, the recalls when they happen, supplier quality issues, approving new suppliers, turnover in operating personnel that creates demand for qualification training, demand for release of new products, et al. The list of negatives is long. It is easy for the person with quality in their job title to quickly become overwhelmed by events. Soon, everywhere they look is darkness with no “light at the end of the tunnel.” The Quality leader must create a common vision of a “brighter tomorrow,” where we have less reactive work to do and more time to focus on being a business partner. Our research has shown that creating a vision and strong tie to strategic business objectives is a key element of a successful transformation.
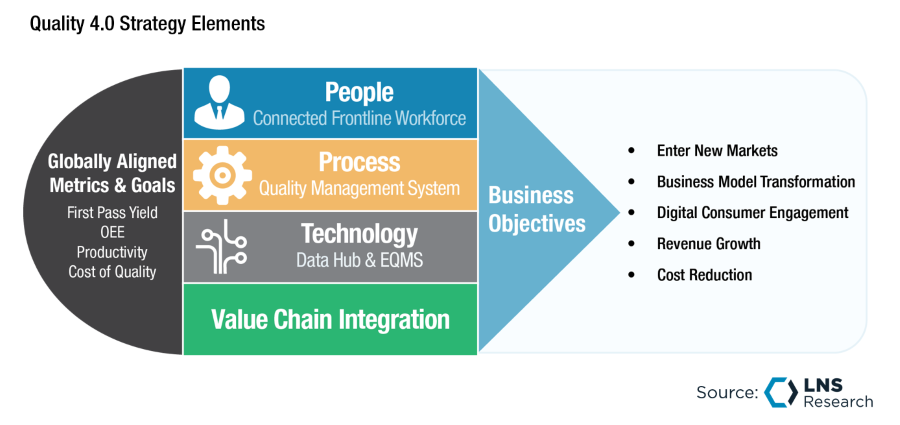
Strategy:
Since Quality 4.0 programs that are technology focused fail, the recommendation is to take a “business forward” approach. Start with the business problems to be solved, rather than what technology to apply. The question of technology does not come to bear until the later half of the Industrial Transformation (IX) framework.
%20Framework%2c%202022%20logo.png?width=1204&name=Industrial%20Transformation%20(IX)%20Framework%2c%202022%20logo.png)
Budget:
A Quality 4.0 transformation that is planned on a shoestring budget will suffer from stops and starts along the journey. This is not ideal from a change management standpoint. Ensure your transformation program is properly budgeted.
Timeline:
Setting unrealistic expectations is one of the quickest ways to lose support when milestones are missed. Our recent Quality 4.0 maturity survey showed that Quality 4.0 leaders view the transformation timeline as five years or more, reflecting the sentiment that Quality 4.0 is not a static end state but a culture change journey.
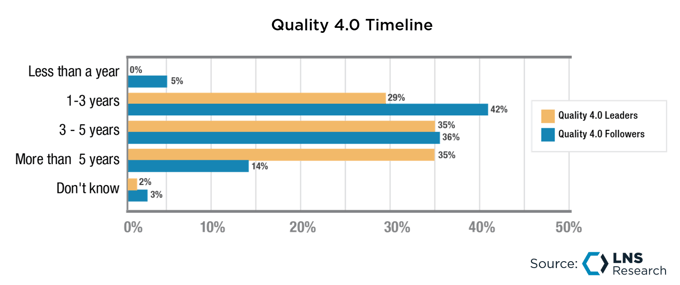
Partnerships and Change Management:
Quality 4.0 programs that succeed are a cross-functional, collaborative effort across the entire value chain. There are some key partnerships that help drive the change. Among them are Human Resources. There is a strong element of the three-pronged approach to transformation around bringing people along for the journey. Human resources is a key partner to set up the policies and practices around role sharing, promotion paths between digital and quality, and most importantly, developing and deploying an effective training program for Quality personnel on digital concepts. Seventy-eight percent of Quality 4.0 leaders have a training program deployed on digital topics. In recent years, availability of digital training tools has made delivering “micro-training” at the point and time of need easier to accomplish than ever before.
Quality leaders need to get in the driver's seat and engage key business partners to achieve the vision of a Quality 4.0 transformation and the ultimate goal of Quality as a valued business partner across the value chain of the business. Don't let a Quality 4.0 transformation happen To you. Eighty percent of Quality transformation leaders report that the Quality Leader is not engaged in the initiative. Transformation is a train that is leaving the station, better to be on it than running to catch it.

All entries in this Industrial Transformation blog represent the opinions of the authors based on their industry experience and their view of the information collected using the methods described in our Research Integrity. All product and company names are trademarks™ or registered® trademarks of their respective holders. Use of them does not imply any affiliation with or endorsement by them.