L2L’s Connected Workforce Summit hosted over 70 companies and 140 attendees in sunny Salt Lake City this May. Registered attendees were given a rare opportunity to join a plant tour at a nearby Young Living, essential oils producer, manufacturing facility, and distribution center. Limited seating was increased due to high demand, with a chartered bus taking 45 attendees to Spanish Fork, UT, to see production and L2L’s connected worker hub, a Connected Frontline Workforce (CFW) solution, in action.
The burning platform for many CEOs is the urgency to create future-ready frontlines to sustain essential business operations. Manufacturing's Industrial Transformation (IX) has enabled decades of step change improvements with steam power, electrical energy, sophisticated electronics, and IT system deployments. As industrial technology matured, manufacturing productivity plateaued, and career desirability declined.
Future of Industrial Work (FOIW) Leaders are finding an employee-centric lifecycle, adopting processes to support the frontline, and integrating human-centric technology. For example, this includes CFW solutions that are aiding manufacturers in attracting, training, and retaining a quality workforce. Aligned initiatives and pursuing emerging technology such as automation, ML, AI, vision systems, robots, and cobots enable FoIW Leaders to achieve significant business value.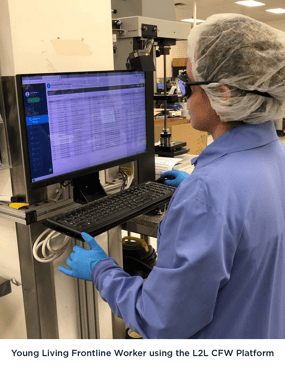
With that in mind, I focused my trip on three key questions:
-
-
-
How is the frontline using the L2L product and other technology within the plant?
-
What are the value drivers for using L2L solutions and attending The Connected Workforce Summit?
-
Which industrial organizations should add L2L to their short list of potential CFW providers?
Shift Culture Faster with the Frontline
Manufacturing leaders recognize that the necessary culture shift requires a proactive, comprehensive approach to building a future-ready frontline to survive skilled labor shortages. L2L event attendees gathered not to commiserate but to share individual journeys to transform the frontline. A commonality was using CFW solutions to boost success and speed of change by creating a connected workforce.
The Young Living tour kicked off the engagement in a familiar setting to ask questions and share ideas. The L2L event was unique in having frontline users attend the event. It was refreshing to hear the frontline say CFW solutions have significantly improved work while shifting operational culture and driving step-change performance.
The customer’s value proposition for CFW included:
-
-
-
Accessible data and information for the work
-
Improved processes with production insights
-
Completing work better and faster with visibility
-
Creation of comprehensive updates without tedious paperwork
Workforce adoption requires a strong people and process focus. L2L’s “born on the shop floor” approach understands user adoption. Future growth will rely on the company’s laser focus on pragmatic solutions and a user interface designed for the frontline. LNS Research recommends solution providers invest in CFWs key capabilities, such as personalized, in-context information, to drive acceptance and remain competitive.
LNS Research Analyst Allison Kuhn speaking at L2L Connected Workforce Summit
CFW Solutions are Removing Transformation Barriers
FOIW Leaders are redefining the nature of work across people, process, and technology and realizing the value of a connected workforce. L2L summit topics focused on what’s driving transformation across the industry and how customers navigate transformation barriers by recognizing the value of a connected workforce.
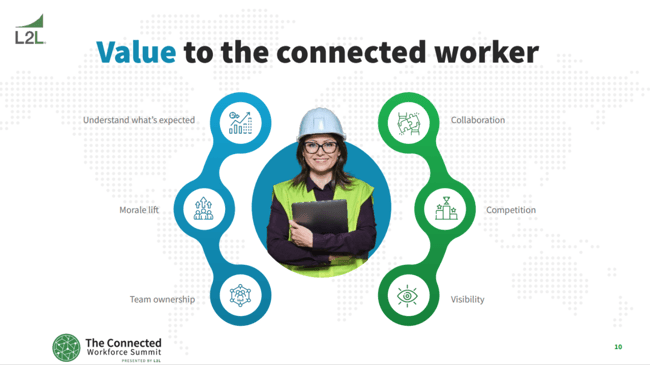
LNS Research's studies show that the top drivers of Industrial Transformation (IX) programs include:
Attendees spanned all stages of transformation maturity, but IX program drivers were mostly aligned. Ease of use, solution flexibility, and quick ROI are common customer selling points. L2L’s strength to date has been a good understanding of what problems customers are trying to solve to market:
-
-
-
Rapid deployment with out-of-the-box functionality
-
Improved workforce adoption rates
-
Real-time visual metrics across the organization
-
Scalable to the enterprise level
Dispatch, the platform hub that unifies the plant and provides visibility to the workforce, is the L2L anchor offering. Expanded offerings include a no-code app creation for users to customize the solution through L2L Studio and AI-assisted in-context workforce recommendations using L2L Assist. The product showcase featured a new module to consolidate plant visualization and digitize collaboration, providing a centralized starting point for effective shift change, recurring meetings, and unplanned event updates.
The growing L2L enterprise should focus on continued opportunities for networking and sharing best practices while gathering insight to update the product roadmap. Essential capabilities such as AI and advanced analytics must mature to stay ahead of market trends and compete against a broad, rapidly evolving CFW technology space.
Deploy, Scale, and Embed with Partners
The strength of L2L’s industry expertise has supported company growth since its founding in 2010. John Davagian, CEO as of 2021, continued to grow the company footprint and portfolio by acquiring Accumine, an AI and IIoT solution provider. Today's customer base is predominantly across Discrete manufacturing; examples include Industrial Machinery & Equipment, Food & Beverage, Aerospace & Defense, Electronics, Consumer Goods, and Building Materials customers.
John Davagian, CEO of L2L, speaking at the L2L Connected Workforce Summit 2023
After deploying Dispatch, many customers find additional modules such as Maintenance, Production, and Connect the next logical step. Expanding the L2L offerings across the plant and enterprise is commonly due to the ease of use and improved results in OEE, throughput, equipment downtime, maintenance spend, and quality costs.
Discrete manufacturers should include L2L on the shortlist of CFW providers. The right provider will be able to support the long-term needs, technology strategy, and overall IX strategy integration to deploy, scale successfully, and embed enterprise-wide. Customers should evaluate a provider’s:
-
-
-
Current offerings and portfolio performance
-
Company growth and product delivery history
-
Product improvements and roadmap strength
-
Customer testimonials and a forum for user engagement
CFW adoption will only accelerate and demand more functionality. L2L should continue developing key CFW capabilities and remain focused on industry expertise on the team to remove transformation barriers and meet what customers have come to expect.
The Dispatch Demo area at the L2L Connected Workforce Summit 2023
Technology won’t overcome the plateau - The good news is that we know what will
CEOs have lost touch with the frontline, and trust is a critical enabler in removing barriers and accelerating strategy. Manufacturing leaders need to accept that transformation must be reinvented to thrive. FOIW Leaders are going beyond digital enablement and realigning people, process, and technology to create significant value.
Frontline jobs are becoming less physical and more sophisticated, with integrated technology increasing across frontline operations (e.g., automation, vision systems, robotics, cobots, and advanced analytics).
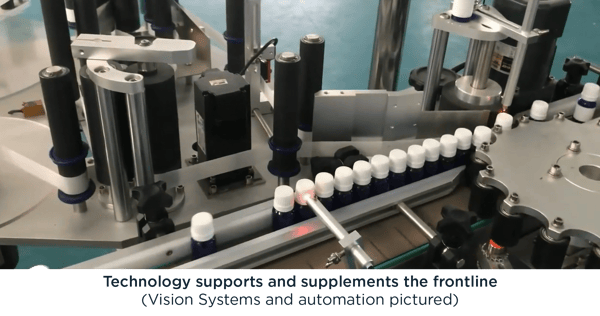
Manufacturers can redefine the nature of work by accepting:
-
-
-
Increasing manufacturing desirability is crucial for future-ready frontlines. The employee lifecycle must be renovated to focus on the total employee experience.
-
FOIWs strategy is table stakes as workforce demographics shift. The holistic approach provides best practices to flip digital technology expectations into a competitive advantage.
-
Best practices are not all created equal. Change management is imperative to navigate the organization's long-standing manufacturing culture and nuances.
-
The cookie-cutter strategy won’t scale. Solution providers can help customers refine the vision, align strategy, and test messaging for successful deployment and scale.
Solution Providers can enable Digital Transformation as the work environment changes by recognizing:
-
-
-
Customers need solutions that frontline workers embrace. Products must support the workforce, identify opportunities, and deliver actionable insight to prove value.
-
The user interface is critical for next-gen solutions to scale and embed enterprise-wide.
-
Pre-built connectors, low-code/no-code capability, and customer support are needed to bridge the skills gap and accelerate transformation.
-
Create provider differentiation with forums to share challenges, lessons, learnings, and best practices.
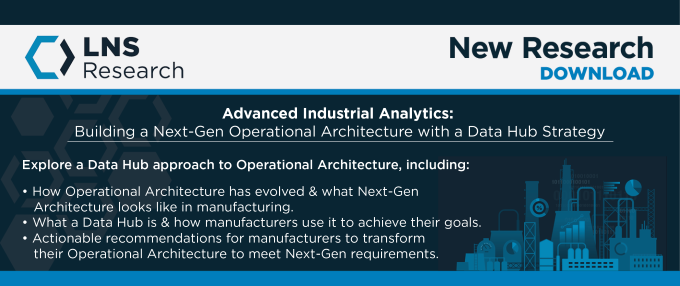